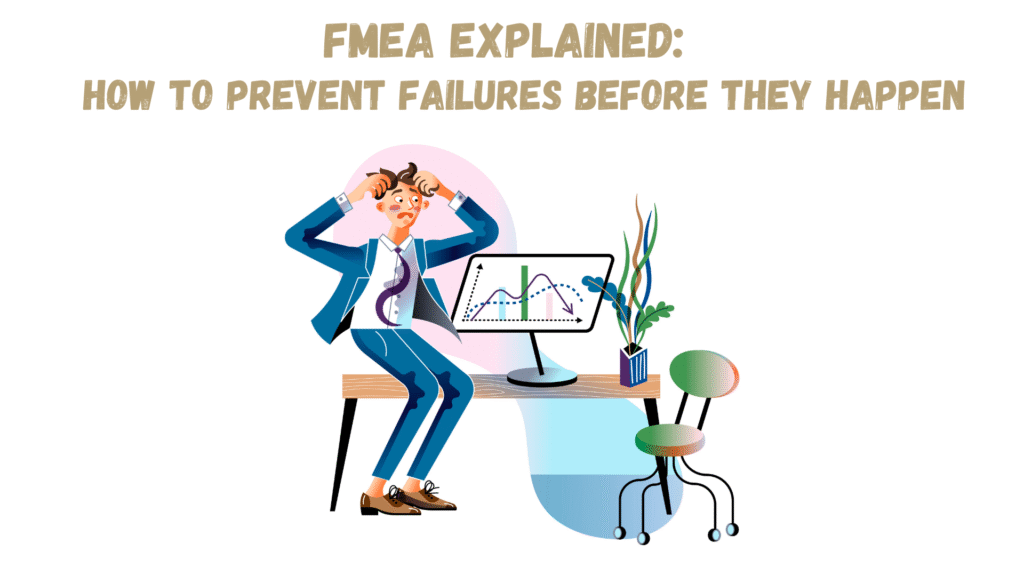
FMEA Explained: How to Prevent Failures Before They Happen
Every product, process, or system, no matter how well-designed, carries a certain level of risk. What separates successful operations from vulnerable ones is the ability to see those risks coming. Failure Mode and Effects Analysis, or FMEA, equips organizations with that foresight.
Used by engineers, quality experts, project managers, and operations teams, FMEA provides a disciplined way to uncover where things might go wrong and to make them right before they ever break. But do not consider FMEA just a tool, it’s a strategy. One that transforms reactive thinking into preventive action.
In this guide, we’ll take a detailed look at FMEA from a fresh perspective. We’ll explore its foundations, how it’s evolving, and the ways it’s being applied in modern industries to build robustness into both products and processes.
The Philosophy Behind FMEA
Before diving into spreadsheets or calculations, it’s important to understand why FMEA exists.
Think of FMEA as a structured conversation, a way for cross-functional teams to ask, “What could go wrong?” and then dig into “Why would that happen?” and “What can we do about it now?”
This proactive mindset means you’re not just reacting to breakdowns or complaints, you’re engineering confidence into your system. That shift is subtle but powerful.
The idea originally came from aerospace and military programs in the mid-20th century, where failure could mean catastrophic loss. Over time, it found its way into automotive, healthcare, electronics, and even software development.
Today, FMEA is part of many quality frameworks.
What Sets FMEA Apart?
Unlike basic checklists or informal reviews, FMEA:
- Is repeatable and structured
- Considers both the cause and the consequence of each risk
- Helps teams focus on the areas with the highest combined risk
- Drives both short-term corrective actions and long-term improvements
- Encourages early detection rather than last-minute fire drills
It doesn’t just ask, “Is something wrong?” It asks, “What if something went wrong here? How bad would it be? Could we catch it in time?”
Types of FMEA: More Than Just Design and Process
The most common forms are:
1. System FMEA
Used to evaluate interactions between subsystems or functions. Often applied early in the product lifecycle.
Example: In aerospace design, a system-level FMEA might explore how a loss of communication from a control module affects multiple systems onboard.
2. Design FMEA (DFMEA)
Focuses on product features, materials, and tolerances. Ideal during the concept or detailed design phase.
Example: A robotics company uses DFMEA to evaluate the risk of a joint failing due to over-torque, then redesigns it with a limiter.
3. Process FMEA (PFMEA)
Analyzes production or service operations. Best applied before or during process development.
Example: A food manufacturer applies PFMEA to packaging lines, discovering that inconsistent sealing temperature can lead to contamination risks.
4. Service FMEA
Addresses failure risks in customer service, technical support, or maintenance environments.
Example: An IT helpdesk uses Service FMEA to reduce the risk of misdiagnosis during remote troubleshooting.
FMEA is also being adapted for software projects, sustainability initiatives, and cybersecurity. Do not relate it to only machines. It’s about managing risk in complex systems, regardless of industry.
FMEA vs. Traditional Risk Assessments
Traditional risk assessments often look at historical data and known issues. FMEA, by contrast, focuses on prediction. It encourages teams to imagine possibilities, even if those issues haven’t occurred yet.
While other tools may tell you what went wrong, FMEA tries to make sure nothing goes wrong in the first place. That forward-thinking nature makes it ideal for innovation-driven fields.
Anatomy of an Effective FMEA
Let’s break down how a well-executed FMEA works, component by component.
Functional Analysis
Begin by understanding what the product or process is meant to do. Functions should be described clearly, not vaguely. If a component’s purpose isn’t understood, its potential failures won’t be either.
Failure Modes
These describe how the function might not be achieved. Don’t limit this to “breaks” or “stops.” Failure can be subtle: intermittent performance, slow response, or deviations that escape detection.
Effects of Failure
What happens next? Does the product shut down? Does the user notice? Could safety or compliance be compromised?
Root Causes
Why would this failure occur? These could involve design assumptions, environmental conditions, operator behavior, or material inconsistencies.
Current Controls
What systems are in place to prevent or detect this failure before harm occurs? How reliable are they?
Evaluation Metrics
Traditionally, three scores are used:
- Severity (S) – how serious the effect is
- Occurrence (O) – how often the cause is expected
- Detection (D) – how likely the current controls will catch it
Risk Priority Number (RPN)
The classic formula is:
RPN = Severity × Occurrence × Detection
High RPNs indicate areas needing attention. However, newer standards emphasize deeper risk judgment rather than relying only on numeric cutoffs.
A Modern Twist: Action Priority (AP)
There’s a new concept called Action Priority (AP) to replace sole reliance on RPN. AP assigns high, medium, or low priority based on severity, occurrence, and detection, without relying on multiplying scores.
This approach encourages more nuanced decisions, especially when high-severity issues are rare but hard to detect. It avoids the trap of ignoring serious problems just because one rating number is low.
Making FMEA Work in Practice
FMEA is easy to understand in theory, but its value depends entirely on how it’s done. Here are strategies that ensure your FMEA effort is effective:
1. Start Early
Use FMEA during design, not after testing. The earlier risks are identified, the cheaper they are to fix.
2. Work Cross-Functionally
Bring in voices from engineering, operations, logistics, customer support, and quality. Each has insights the others may miss.
3. Use Field Data to Inform Ratings
Severity should reflect real-world impact. Occurrence ratings improve with access to warranty data, complaint logs, or SPC trends.
4. Keep It Living
FMEA should evolve. Update it with every design change, customer issue, or process improvement. A static FMEA quickly becomes obsolete.
5. Link It to Corrective Action
Don’t just identify risks, act on them. If a critical risk is discovered, your improvement plan should reflect it with clear owners and timelines.
A Different Take: What FMEA Doesn’t Solve Alone
Although FMEA is powerful, it isn’t a one-size-fits-all solution. It excels when paired with other quality tools such as:
- Root Cause Analysis – to investigate failures that did occur
- Control Plans – to translate FMEA learnings into daily checks
- Fault Tree Analysis – for mapping system-level cause-and-effect chains
FMEA is strongest as a thinking tool. It helps clarify risks, align teams, and structure actions. But ultimately, its success depends on how rigorously it’s applied and whether leadership treats its outputs seriously.
Final Thoughts
FMEA is more than a worksheet. It represents a culture where failure is anticipated, not feared, where teams collaborate to find cracks before they spread.
The most effective organizations embed FMEA thinking into their DNA. Whether launching new products, improving services, or reshaping operations, they ask the same three questions:
- What could go wrong?
- How would we know?
- What can we do today to avoid that tomorrow?
That’s the heart of proactive quality.