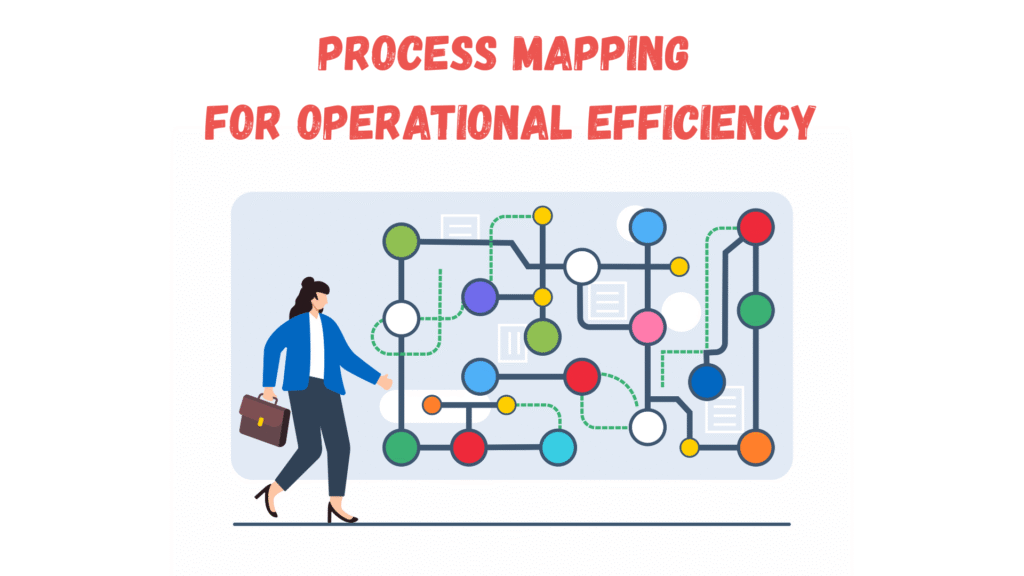
Process Mapping for Operational Efficiency
Operational efficiency doesn’t just happen. It’s built, layer by layer, through clarity, alignment, and continuous improvement. One of the most powerful tools in this journey is process mapping. At its core, process mapping is about drawing out how work gets done, step by step, visually and clearly. But it’s far more than a diagram. It’s a way to uncover bottlenecks, simplify complex workflows, and engage teams in meaningful improvement.
In this guide, we’ll explore what process mapping is, the different types of maps, how to create one, and how it can transform operations in any industry. Whether you’re in manufacturing, healthcare, finance, or IT, process mapping offers a structured path to better performance.
What is Process Mapping?
Process mapping is the act of visually representing the steps in a workflow. It outlines what tasks are performed, by whom, in what sequence, and using which tools or systems. It’s a practical method to describe how a process flows from beginning to end.
Think of it as a flowchart for business operations. But unlike a simple checklist, a process map provides a more holistic view. It shows decision points, handoffs between departments, dependencies, and even potential problem areas.
When well-executed, process maps serve multiple purposes:
- They clarify how work is actually being done.
- They align teams around a shared understanding.
- They highlight inefficiencies, redundancies, or risks.
- They lay the groundwork for automation, standardization, or redesign.
Why Process Mapping Matters for Operational Efficiency
Operational efficiency is about doing more with the same or fewer resources, while maintaining quality and consistency. Process mapping supports this goal in several strategic ways:
1. Revealing Hidden Waste
Even in high-performing organizations, there are invisible inefficiencies: delays between handoffs, duplicated efforts, and unnecessary steps. A process map exposes these issues in a visual, non-blaming way, making it easier for teams to collaborate on improvements.
2. Enhancing Communication
Different people may describe the same process in very different terms. Mapping creates a single, shared picture. It breaks down silos and promotes cross-functional understanding, especially useful during change initiatives or onboarding.
3. Standardizing Best Practices
Once a process is mapped and optimized, it becomes a living standard. New employees can be trained faster. Quality becomes more predictable. Compliance becomes easier to demonstrate.
4. Supporting Digital Transformation
Before you automate a process, you must understand it. Process mapping helps organizations determine which processes are worth automating and how they should be structured for digital tools to deliver maximum value.
Types of Process Maps
Not all process maps are the same. Depending on your goals and the complexity of the process, different types of maps may be used.
1. Flowchart (Basic Process Map)
This is the most common type. It uses standard symbols, rectangles for tasks, diamonds for decisions, arrows for direction. It’s ideal for documenting simple workflows or sub-processes.
2. Swimlane Diagram
A swimlane map divides the process into lanes, each representing a department, team, or role. This format is excellent for showing responsibilities and handoffs across functions.
3. Value Stream Map (VSM)
Used heavily in Lean and manufacturing environments, a VSM shows both process steps and the flow of materials and information. It highlights value-added versus non-value-added time, helping teams reduce cycle time and waste.
4. SIPOC Diagram
SIPOC stands for Suppliers, Inputs, Process, Outputs, and Customers. This high-level map is useful during the early stages of process improvement to define boundaries and stakeholders.
5. High-Level vs. Detailed Maps
High-level maps show the major phases of a process, while detailed maps zoom in on each activity. Both are useful, depending on whether you’re scoping a project or driving deep operational changes.
Key Elements of a Good Process Map
A strong process map does more than just connect boxes and arrows. It must include:
- Start and End Points: Every map needs a clear beginning and conclusion.
- Tasks/Activities: Each step should describe an action, not a vague label.
- Roles or Functions: Who performs the task? This adds accountability.
- Decision Points: Represented by diamonds, these show where choices are made.
- Flow Direction: Arrows must clearly show how the process progresses.
- Inputs and Outputs: What triggers the process, and what does it produce?
For more advanced maps, additional elements like cycle time, wait time, or error rates can be added to support performance analysis.
How to Create a Process Map: Step-by-Step
Whether you’re mapping a simple task or a complex system, these steps provide a reliable structure:
Step 1: Define the Scope and Purpose
Decide which process to map and why. Are you trying to reduce errors, speed up service, or prepare for automation? Set clear boundaries to avoid scope creep.
Step 2: Assemble a Cross-Functional Team
Involve people who actually do the work, not just managers or process owners. Their insights reveal the reality, not just the theory of how things operate.
Step 3: Document the Current (“As-Is”) Process
Use sticky notes, whiteboards, or mapping software. Focus on what happens today, not what should happen. Walk through each step in order and include decision points.
Step 4: Validate the Map with Stakeholders
Once the draft is ready, walk through it with others involved in the process. Look for missing steps, misunderstandings, or exceptions that may not have been captured initially.
Step 5: Analyze for Efficiency Gaps
Ask questions like:
- Where do delays occur?
- Are any steps duplicated?
- Are approvals taking too long?
- Where do errors frequently happen?
This is where operational inefficiencies start to surface.
Step 6: Design the Future (“To-Be”) Process
Now that you understand the current state, you can redesign it. Eliminate waste, streamline handoffs, and introduce standardization where needed. This redesigned map becomes the goal for improvement efforts.
Step 7: Implement and Monitor
Change doesn’t end with a map. Document procedures, train teams, monitor key metrics, and adjust the process as needed. The map should evolve as improvements are made.
Tools and Technologies for Process Mapping
Modern organizations use various tools to create, share, and maintain process maps. Some popular options include:
- Microsoft Visio: A classic diagramming tool with wide adoption in corporate environments.
- Lucidchart: A cloud-based solution that supports real-time collaboration.
- Bizagi: Offers advanced business process modeling capabilities.
- Miro or MURAL: Digital whiteboards that are great for remote mapping sessions.
- BPMN Tools (e.g., Signavio, ARIS): Business Process Model and Notation (BPMN) tools for enterprise-level process documentation.
Even simple tools like PowerPoint or hand-drawn maps can be effective if clarity and collaboration are maintained.
Common Mistakes to Avoid
To ensure your process mapping initiative delivers results, watch out for these common pitfalls:
- Mapping an ideal process instead of the real one.
- Involving only managers, not front-line staff.
- Making the map too complex or hard to read.
- Ignoring exceptions and edge cases.
- Failing to update the map after changes.
A map is most useful when it reflects reality and serves as a living document. Keep it updated and visible to the teams that use it.
Process Mapping and Continuous Improvement
Process mapping is not a one-time event. It’s a recurring activity tied to a culture of improvement. Organizations that embed process thinking into their DNA benefit from:
- Faster decision-making
- Higher employee engagement
- Improved service delivery
- Better adaptability to change
Lean, Six Sigma, and Agile all incorporate process mapping as a foundational tool. In fact, most structured problem-solving frameworks (such as DMAIC or PDCA) begin with mapping the current state.
Final Thoughts
Process mapping offers more than operational clarity. It’s a strategic lens for continuous improvement. When you can see how work flows, you can improve it. And when you improve it, you drive performance, reduce delays, and empower teams.
For leaders seeking higher efficiency, lower costs, or stronger collaboration, process mapping is a practical place to start. It aligns people, tools, and outcomes in a visual story that anyone can follow and everyone can improve.
Start with one process. Map it. Walk through it. Refine it. Repeat. The road to operational excellence is built one mapped process at a time.