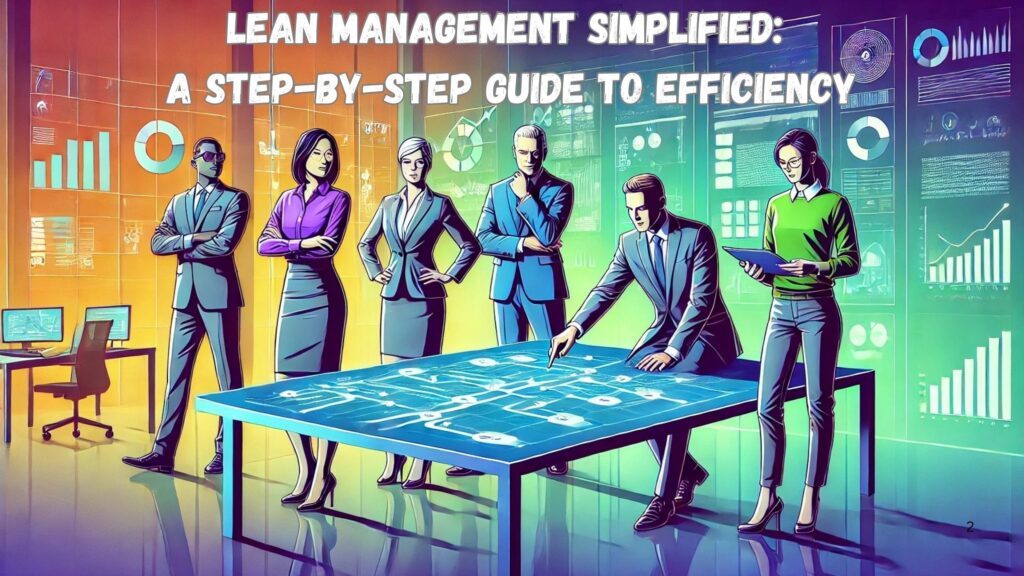
Lean Management Simplified: A Step-by-Step Guide to Efficiency
Lean management is one of the most misunderstood business strategies out there. You’ve probably heard the promise: “Reduce waste, increase efficiency, and boost productivity.” But here’s the thing—most companies try to implement lean principles and fail miserably.
Why? Because they think lean is just about cutting costs and getting rid of “extra” resources. But lean isn’t about doing more with less. It’s something more. It’s about doing the right things, the right way, at the right time.
And when you get it right? The results will be staggering.
But lean isn’t magic. It’s a methodical process that requires discipline. It starts with understanding waste, mapping out inefficiencies, and optimizing workflows.
That’s exactly what we’ll cover in this step-by-step guide. Let’s get into it.
Step 1: Identifying the 8 Wastes in Modern Business
Lean management is all about waste reduction. But first, you need to spot it.
Toyota, the company that pioneered lean, identified eight deadly wastes that silently destroy productivity improvement.
You’re dealing with most of them right now.
So, it’s better to know about those wastes first.
1. Defects Waste:
These are the wastes that are not upto the mark of the customers.
This could be:
- Incorrect product delivered to customers.
- A wrong invoice that needs corrections.
- A bug in software that needs fixing.
Every defect wastes time, money, and energy.
2. Overproduction Waste:
This is a big one. Overproduction means producing too much or too soon. In businesses, it could be:
- Generating excessive reports that no one reads.
- Manufacturing more products than demand requires.
- Developing features customers don’t actually use.
Too much work creates clutter, leading to confusion, delays, and wasted effort.
3. Waiting Waste:
These wastes happen when there is a delay in the workflow.
Such wastes happen when you wait for approvals, responses, or materials.
Common culprits:
- Waiting for decisions from management.
- Holding tasks hostage while waiting for feedback.
- System delays (slow software, outdated tools).
Waiting kills momentum and turns productive time into dead time.
4. Unused Talent Waste:
This is one of the most overlooked wastes. It happens when your employees have skills, insights, and ideas, but they are not being used effectively.
Common signs of unused talent:
- Employees are stuck doing mundane tasks instead of valuable work.
- Ideas are ignored because there’s no system to capture them.
- No opportunities for growth, which leads to disengaged teams.
Such waste results in low morale and lost innovation
5. Excess Transportation Waste:
Every time a document, file, or product moves between people or locations unnecessarily, it adds waste. Such waste in Lean management is known as excess transportation waste.
Examples:
- Multiple handovers in an approval chain.
- Shuffling paperwork between departments.
- Unnecessary back-and-forth emails.
Apart from wasting time, excess transportation increases the chance of errors, too.
6. Excess Inventory Waste:
As the name says, excess inventory is all about storing more than necessary.
In service businesses, it looks like:
- Too many open projects at once.
- Unfinished work piling up.
- An overflowing backlog with no clear prioritization.
Holding onto too much “work-in-progress” creates stress, confusion, and delays.
7. Unnecessary Motion Waste:
If people have to search for information, jump between tools, or move back and forth to complete a task, it’s a wasted effort.
Examples:
- Employees spend time looking for documents.
- Switching between apps too often.
- Manually entering data into multiple systems.
Other examples of such waste include lifting, bending, and reaching from one point to another.
8. Extra Processing:
It’s about doing more than what’s needed. If a customer only needs a simple answer, but you provide an in-depth report, that’s extra processing.
Other examples:
- Unnecessary approvals in workflows.
- Too many reviews before sending an email.
- Over-complicating simple tasks.
The solution? Keep things simple and only do what’s necessary to get the best result.
Step 2: Value Stream Analysis Fundamentals
Once you’ve identified the wastes, the next step is to map out your processes and visualize where value is added and where it’s not. To do this, you need to know about Value Stream Analysis (VSA).
What is Value Stream Analysis?
Value Stream Analysis (VSA) is a lean tool that helps businesses see how materials and information move through a process to deliver a product or service to customers.
By drawing out each step in a process, businesses can spot areas where work slows down, gets duplicated, or doesn’t add value.
For example, imagine a coffee shop where orders are written on paper before being entered into a computer. If baristas waited for the computer entry before making the coffee, this extra step would slow everything down. However, with VSA, the shop could remove the paper step and have orders go directly into the system, making service faster.
How to Conduct a Value Stream Analysis?
- Step 1: Map Out Your Current Workflow
- Document the entire process from start to finish. How does work move through your system? Where do delays happen?
- Step 2: Identify Value vs. Waste
- Separate value-adding activities (things customers are willing to pay for) from wasteful steps (delays, excess movement, overprocessing).
- Step 3: Spot Bottlenecks
- Find where work piles up, approvals slow things down, or inefficiencies creep in.
- Step 4: Redesign for Lean Efficiency
- Create a new, optimized workflow that removes waste while keeping essential steps intact.
- Step 5: Implement and Monitor Changes
- Lean isn’t a one-time job. It’s a continuous improvement cycle. Track performance, gather feedback, and refine the process over time.
Step 3: Implementation of 5S Methodology
A disorganized workspace is one of the biggest hidden productivity killers. Employees waste time searching for tools, documents, or files, leading to frustration and inefficiency.
This is where the 5S methodology can help you.
What’s that? It consists of five “S” approaches that organize a workplace.
Here are they:
- Sort (Seiri) – Getting rid of everything that isn’t needed. Declutter ruthlessly.
- Set in Order (Seiton)– Arranging tools, files, and equipment so they’re easy to find and use.
- Shine (Seiso)– Keeping everything clean and well-maintained.
- Standardize (Seiketsu) – Making organization a habit, not a one-time cleanup.
- Sustain (Shitsuke)– Ensuring long-term consistency with regular checks and improvements.
Step 4: Standard Work Development
After organizing, it’s time for efficiency. To improve efficiency, businesses must ensure that every task is done in the best, most efficient way possible.
Benefits of Standard Work:
- It Ensures tasks are performed consistently, leading to predictable outcomes.
- It Provides a clear reference for onboarding new employees.
- It serves as a baseline for identifying areas of enhancement.
Steps to Develop Standard Work:
- Study the current best practices and document each step in detail.
- Involve team members in the documentation process to capture practical insights and foster buy-in.
- Implement the documented procedures, gather feedback, and make necessary adjustments.
- Ensure all employees are trained on the standard work procedures and understand their importance.
To take this a step further, Visual Management Systems help keep teams aligned by making work progress visible and easy to track.
Step 5: Visual Management Systems
If you can’t see a problem, you can’t fix it. That’s why visual management is a key pillar of Lean.
What Is Visual Management?
Visual Management uses charts, dashboards, and simple colour-coded tools to show progress in real-time. It eliminates the need for long meetings, endless reports, and constant check-ins.
Examples of Visual Management in Action
- Kanban boards – These visually track the progress of tasks in real-time.
- Color-coded workflow Indicators– Green means good, yellow means action needed, and red means urgent.
- Performance Dashboards – Show key metrics in real-time.
When problems become visible instantly, they get fixed faster. No more missed deadlines, lost emails, or unclear priorities.
Step 6: Pull Systems and Kanban Integration
One of the biggest problems in most workplaces? They use push systems, where work is forced through the process regardless of demand. This often results in barriers and overworked employees.
Therefore, lean management promotes pull systems. A pull system ensures that work is only started when needed, reducing unnecessary work-in-progress.
Now, Kanban, a visual tool, makes Pull Systems work faster. If you’ve ever seen a Kanban board, you know the basic idea:
- To Do – Tasks waiting to be started.
- In Progress – Tasks actively being worked on.
- Done – Completed tasks.
For Example, A team can only work on three tasks at a time. New tasks can’t start until one is completed. This keeps work balanced, prevents bottlenecks, and improves efficiency.
Step 7: Employee Engagement in Lean
Lean Management isn’t just about processes. It’s about people. If employees don’t get into the system, Lean initiatives fail.
How to Get Employees Engaged in Lean?
- You have to encourage employee feedback.
- You have to provide lean training to the employees.
- You have to recognize their efforts and reward their contributions.
- You have to create a continuous improvement culture.
When employees feel heard and empowered, Lean becomes a shared mission, not just another business strategy.
Step 8: Measuring Lean Success
If you can’t measure it, you can’t improve it. To sustain lean improvements, track these key lean metrics:
1. Cycle Time – This shows how fast work gets done
- Formula: Time from task start to finish.
- Lower Cycle Time = Faster Workflow.
2. First Pass Yield (FPY) – This tells how many tasks are done right the first time
- Formula: Percentage of tasks completed without rework.
- Higher FPY = Fewer Mistakes, Higher Efficiency
3. Lead Time – This signifies how quickly you deliver
- Formula: Time from order placement to delivery.
- Lower Lead Time = Faster Customer Satisfaction.
4. Overall Equipment Effectiveness (OEE) – This reflects how well machines perform
- Formula: Availability × Performance × Quality.
- Higher OEE = More Output with Less Downtime.
Such metrics can give you an idea of the overall productivity improvement of the business.
Final Thoughts
Lean Management is not a quick fix. It’s a step-by-step transformation that eliminates waste, improves efficiency, and enhances productivity. Follow these eight structured steps, and your business will see lasting success and continuous improvement.
Are you ready to start your Lean journey? Take the first step today!