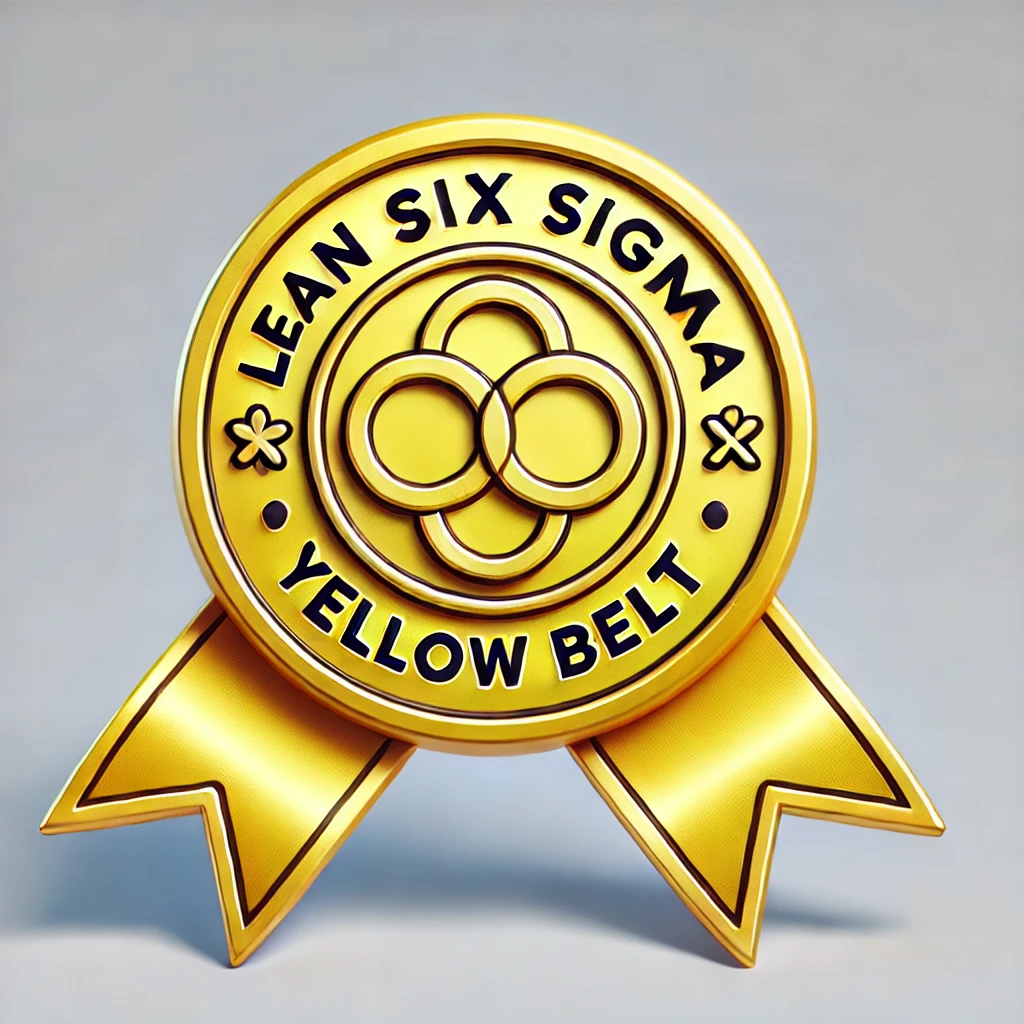
Yellow Belt Certification: The Skill That Sets You Apart in 2025
You sit at your desk, staring at the endless stream of emails, reports, and notifications. Another delay. Another unexpected issue. Another fire to put out.
No matter how hard you try to stay ahead, something always slips through the cracks. Approvals take too long. Errors keep popping up. The same inefficiencies slow things down—again and again.
You wonder if it’s just the way things are.
But deep down, you know it shouldn’t be this hard.
The real problem isn’t a lack of effort. It’s the way work flows—or rather, the way it doesn’t.
That’s where Lean Six Sigma Yellow Belt training comes in.
It’s not any random Six Sigma certification. It’s a structured way of solving problems before they spiral out of control. A way to see inefficiencies, eliminate waste, and make processes flow smoothly—without adding more work.
And in 2025, when businesses are automating everything in sight, knowing how to optimize processes before they scale is more valuable than ever.
What Is a Lean Six Sigma Yellow Belt?
A Lean Six Sigma Yellow Belt is more than an entry-level certification.
It’s a practical skill set—a way to identify inefficiencies, reduce delays, and improve processes without increasing costs.
Think of an organization like a high-performance engine.
- Black Belts and Green Belts design the system-wide strategies.
- Yellow Belts keep everything running smoothly.
Without Yellow Belts, there’s no real-time data, no visibility into process bottlenecks, and no structured way to solve daily problems.
A strong Yellow Belt professional doesn’t just follow instructions—they analyze workflows, spot hidden inefficiencies, and use structured methodologies to fix them permanently.
Most importantly, Yellow Belt skills help you to bridge the gap between leadership and execution. They make sure solutions aren’t just theoretical but actually work in the real world.
And the best part? These skills aren’t limited to manufacturing. Whether you work in healthcare, finance, technology, or customer service, a Yellow Belt makes you a problem solver—the kind of professional every business wants.
What You’ll Learn in a Lean Six Sigma Yellow Belt Course
Yellow Belt training isn’t about memorizing concepts.
It’s about applying them—learning to see inefficiencies and fix them for good.
1. The Foundation: Understanding Lean & Six Sigma
Most businesses struggle because they don’t follow a structured way to solve problems.
Lean and Six Sigma work together to change that:
- Lean eliminates waste—cutting unnecessary steps, reducing delays, and making work flow smoothly.
- Six Sigma reduces variation—ensuring consistency, minimizing errors, and improving quality.
Together, they turn businesses into well-oiled machines.
But before you can fix anything, you need to understand how things really work.
That’s why the next step is process mapping.
2. Process Mapping: Seeing What’s Really Happening
Most workflows seem efficient—until you break them down step by step.
Then the cracks start to show.
- Why are three different departments reviewing the same document?
- Why does an order sit in limbo for two days before moving forward?
- Why does customer support get flooded with the same complaint over and over?
The answers are hidden inside the flow of work.
Mapping out a process—visually breaking down each step—reveals inefficiencies no one noticed before.
And once you see them?
You can’t unsee them.
3. Identifying the 8 Wastes: What’s Slowing You Down?
If a process isn’t running smoothly, waste is hiding somewhere inside it.
Yellow Belt training teaches you to spot and eliminate these eight common types of waste:
- Defects: Rework, errors, and mistakes that slow everything down.
- Overproduction: Making more than needed, leading to wasted time and storage space.
- Waiting: Delays caused by approvals, system lags, or missing information.
- Non-utilized talent: Employees with skills that aren’t being used effectively.
- Transportation: Unnecessary movement of materials, paperwork, or information.
- Inventory: Overstocking products, leading to waste and storage issues.
- Motion: Unnecessary steps or movements that add no value.
- Extra Processing: Doing more work than required due to unclear requirements or poor planning.
Once you learn to see waste, you can start eliminating it.
But spotting problems isn’t enough.
You need a structured way to solve them.
4. The DMAIC Framework: Solving Problems the Right Way
Most teams fix symptoms instead of real problems.
- The report is late? “Let’s set an earlier deadline.”
- Too many product defects? “Let’s work faster.”
- Customers keep complaining? “Let’s train the support team better.”
But none of those solutions fix the root cause.
That’s why this quality management training includes DMAIC, a structured problem-solving method:
- Define: Identify the real problem—not just the symptoms.
- Measure: Collect relevant data to understand how bad the problem really is.
- Analyze: Find the root cause—because fixing the wrong problem is worse than doing nothing.
- Improve: Implement tested solutions—no guesswork, no trial and error.
- Control: Set up systems to make sure improvements don’t fade over time.
Because real solutions don’t just patch problems.
They eliminate them for good.
Why a Yellow Belt Certification Matters in 2025
Businesses are changing fast. AI, automation, and digital tools are reshaping how work gets done.
And here’s the truth:
Automation doesn’t fix broken processes. It just magnifies the problems.
A flawed workflow running at 10x speed doesn’t become efficient—it becomes a disaster.
That’s why businesses in 2025 aren’t just looking for employees who work hard.
They need people who know how to optimize processes before they scale.
And that’s exactly what a Yellow Belt does.
Here’s why it matters now more than ever:
1. AI and Automation Are Changing the Workplace
Automation speeds up processes, but if those processes are inefficient to begin with, automation just magnifies the waste.
A Yellow Belt ensures workflows are optimized before technology takes over, preventing waste from scaling.
2. Cost Reduction Without Sacrificing Quality
Many businesses cut costs the wrong way—by reducing headcount or slashing budgets.
The real savings come from eliminating inefficiencies—not reducing productivity.
Lean Six Sigma ensures that cost-cutting improves efficiency, rather than creating more problems.
3. Remote and Hybrid Work Requires Process Optimization
Virtual teams struggle with delays, miscommunication, and unnecessary meetings.
Lean Six Sigma streamlines digital workflows, automates approvals, and reduces bottlenecks, making remote work smoother.
4. Companies Demand Cross-Functional Skills
Employers don’t just want specialists anymore. They want professionals who can analyze data, solve problems, and improve processes across multiple departments.
A Yellow Belt helps you become a decision-maker, not just an executor.
Final Thoughts: Should You Get Certified in 2025?
If you want to stay ahead, problem-solving is the skill that sets you apart.
Businesses don’t just need more employees. They need people who make things work better.
A Lean Six Sigma Yellow Belt certification is not only a process improvement certification.
It’s a mindset shift. A way to see what others miss. A skill set that makes you indispensable.
So the real question isn’t whether this certification is worth it.
It’s are you ready to take the next step?