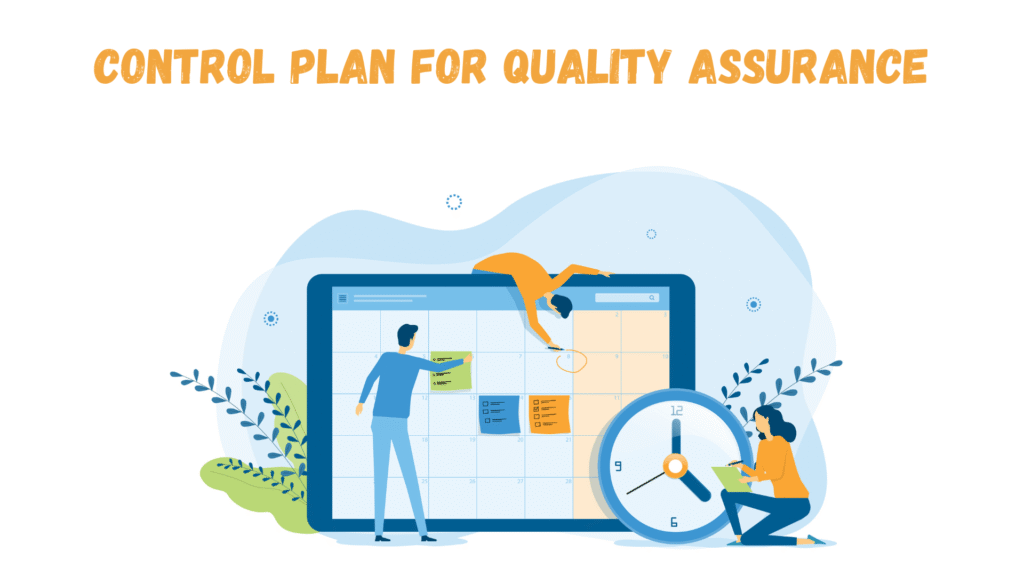
Control Plan for Quality Assurance
Imagine a world where every product rolling off the line meets customer expectations. A world where process hiccups rarely occur because teams know exactly what to watch, when to check, and how to react when something looks off. This level of confidence doesn’t come from good intentions alone. It relies on a tool that many professionals overlook until quality becomes a problem: the control plan.
A well-developed control plan is more than a document; it’s a blueprint for maintaining process control, minimizing variation, and delivering repeatable outcomes. While its roots lie in manufacturing, its value extends far beyond the shop floor, reaching into services, logistics, and any operation where quality assurance matters.
In this guide, let’s break down what makes a control plan effective, why it remains crucial even in today’s high-tech environments, and how you can build one that works for your unique process.
What Is a Control Plan?
A control plan is a structured document that outlines the critical product and process characteristics, the methods to monitor and control them, and the reaction plan if deviations occur. Think of it as a living playbook that ties together design requirements, customer expectations, and day-to-day operational checks.
In a typical control plan, you’ll see elements like:
- Process step description
- Critical characteristics (both product and process)
- Measurement methods and tools
- Control methods (like control charts or go/no-go gauges)
- Frequency of checks
- Responsible persons
- Reaction plans for non-conformities
It acts as a single source of truth for operators, engineers, and quality professionals, ensuring that everyone aligns on what’s important and how to sustain it.
The Origin and Evolution of Control Plans
The control plan concept gained traction in the automotive industry, thanks in part to the rise of Advanced Product Quality Planning (APQP). Original Equipment Manufacturers (OEMs) demanded suppliers prove they could maintain consistency at scale. The control plan offered an auditable document to show how processes were kept in check.
Over time, the idea spread to other industries. Whether producing circuit boards, surgical instruments, or customer support services, the principles stay the same: identify what matters, monitor it effectively, and react appropriately when reality drifts from the plan.
Why Control Plans Matter More Than Ever
In an age of automation, AI, and advanced analytics, some might wonder if the humble control plan has become obsolete. But here’s the truth: while technology enables better data collection and real-time feedback, it can’t replace human discipline and process knowledge.
A strong control plan:
- Bridges the gap between design and production.
- Reduces process variation, the root cause of many defects.
- Enhances training for new operators and team members.
- Builds confidence during customer audits.
- Serves as a foundation for continuous improvement.
Think of it as the safety net that catches issues before they escalate. Even the most sophisticated systems can drift out of control without clear checkpoints and defined reactions.
Key Elements of an Effective Control Plan
Not all control plans deliver the same results. Some gather dust in filing cabinets, while others guide daily operations. The difference often lies in how well the plan is crafted and how actively it’s used.
Let’s break down what separates a high-value control plan from a box-ticking exercise.
1. Clear Process Flow Mapping
A control plan must tie directly to the process flow diagram (PFD) and Failure Modes and Effects Analysis (FMEA). If these foundational documents are misaligned, gaps emerge, and critical controls can be overlooked.
When creating or updating your plan, ensure each process step reflects reality. Walk the line. Talk to operators. Confirm that what’s on paper mirrors what happens in practice.
2. Identification of Critical Characteristics
Not every characteristic deserves the same level of scrutiny. Focus should rest on critical-to-quality (CTQ) characteristics that impact safety, function, regulatory compliance, or customer satisfaction.
Use tools like FMEA to rank potential failure modes by severity, occurrence, and detection. Prioritize your controls accordingly.
3. Defined Measurement Methods and Tools
Specify how each characteristic will be measured or inspected. Include details like:
- Type of measurement tool (e.g., micrometer, vision system)
- Required calibration status
- Sampling plans (how many units, how often)
Clarity here reduces ambiguity and ensures consistency across shifts and operators.
4. Control Methods That Suit the Process
Decide how to maintain control. This could include statistical process control (SPC) charts, mistake-proofing (poka-yoke) devices, or standardized work instructions. The right method depends on the nature of the characteristic and how much variation the process naturally exhibits.
5. Reaction Plans
Even the best controls can’t guarantee perfection. A reaction plan outlines what to do when a measurement drifts out of specification or a process goes unstable.
Who gets informed? Should production stop? What happens to suspect material? These answers must be crystal clear to prevent problems from snowballing.
Types of Control Plans
Every product journey follows a lifecycle, from sketches on a drawing board to the finished item in a customer’s hands. Across that journey, risks, variables, and uncertainties shift. This is why a single, rigid approach to control planning rarely works. Different phases of development need unique control plans that match the level of process maturity and the risks involved.
Let’s unpack each type of control plan more thoroughly so you can understand when to use them, what they look like in practice, and how they evolve as your process matures.
Prototype Control Plan
Think of the prototype control plan as the guiding light during a period of exploration and experimentation. At this stage, you’re working with new materials, unproven methods, and parts that may still change based on design tweaks. Variation is common, so the plan’s focus is to confirm whether your ideas translate well from design to a physical part or service.
In practice, a prototype control plan will include:
- Dimensional Checks: Are the parts or outputs aligning with initial design tolerances? Even if you’re producing single-digit quantities, these early checks help spot feasibility challenges.
- Material Verifications: For products involving advanced alloys, specialized plastics, or unique coatings, validating material integrity early prevents costly surprises later.
- Functional Tests: Prototypes often undergo intense functional testing to uncover hidden weaknesses. This means the plan might specify special inspections, non-destructive testing, or stress testing methods.
- Flexibility for Change: Because design iterations happen fast at this stage, the plan should be light enough to adapt without causing unnecessary administrative burden.
Engineers often work side by side with designers and operators, revising the plan almost daily. It’s less about repeatability now and more about learning what works.
Pre-Launch Control Plan
Once you transition beyond prototypes and start gearing up for real production, the stakes grow higher. The pre-launch control plan acts like a dress rehearsal for full-scale manufacturing. This is where you lock in the process flow, validate capability, and ensure you can deliver consistent parts or services at planned volumes.
Key features of a robust pre-launch control plan include:
- Process Capability Studies: Unlike the prototype phase, you’re now studying process variation statistically. Control charts, capability indices (Cp, Cpk), and machine studies help confirm your processes perform within required tolerances under realistic conditions.
- Initial Production Runs: Often called pilot runs, these batches are larger than prototypes but smaller than full production volumes. The plan should define sampling frequency and inspection points to catch early patterns of variation.
- Enhanced Reaction Plans: You’re moving closer to customer delivery. If an issue surfaces, everyone should know how to respond to prevent suspect batches from reaching downstream customers.
- Feedback Loops: The pre-launch plan should integrate with corrective action processes and lessons learned. Insights gathered here directly shape the final production control plan.
Organizations that skip or rush this stage often encounter costly surprises after launch. Taking the time to run a solid pre-launch plan builds confidence among operators, suppliers, and even customers who may require proof of your production readiness.
Production Control Plan: Sustaining Performance Day After Day
Once the process reaches stability, the production control plan becomes the backbone of daily operations. This is the document operators consult to ensure that every action they take aligns with customer expectations and regulatory requirements.
But there’s more to this stage than just checking boxes. A mature production control plan should:
- Define Roles and Responsibilities Clearly: Operators, inspectors, and supervisors must know who checks what, when, and how. This helps maintain consistency across shifts, suppliers, or sites.
- Embed Statistical Process Control (SPC): If your process runs high volumes, SPC is invaluable for spotting trends and taking corrective action before parts drift out of spec.
- Include Preventive Maintenance Triggers: Some production control plans incorporate triggers for maintenance activities. For example, if a measurement trend signals tool wear, the plan might direct an operator to change a tool insert before defects occur.
- Tie to Error-Proofing Measures: Where possible, integrate poka-yoke devices that prevent human errors altogether. The control plan should reference these measures and detail what to check if they fail.
- Stay Connected to Continuous Improvement: The production plan is not static. Lean teams or Six Sigma projects often use it as a baseline, layering on new insights as they reduce variation or streamline steps.
An effective production control plan empowers operators. Instead of relying on a manager to spot every issue, frontline teams use the plan to self-check, adjust, and maintain control independently.
Seeing It in Action: How Companies Transition Across Plans
It helps to visualize how these control plans overlap rather than stand alone. Take, for example, an automotive parts supplier developing a new fuel injector:
- During the prototype stage, they might produce just a few pieces to test spray patterns and tolerances.
- In pre-launch, they ramp up to a few thousand units, monitoring how real-world manufacturing affects consistency and tool life.
- When they move into full production, the control plan formalizes sampling frequencies, SPC charts for flow rates and dimensions, and actions operators must take when control limits signal a potential drift.
This progression helps companies avoid jumping straight from idea to full-scale production without a safety net. Each stage builds process knowledge, strengthens operator confidence, and protects the end customer from surprises.
Adapting Control Plans for Services and Transactional Work
While the concept is rooted in manufacturing, the staged approach applies well to non-manufacturing processes too. In software development, for instance, a prototype control plan could govern early code validation and user experience testing. A pre-launch plan might include stress testing, beta user feedback, and system integration checks. Once live, the production plan focuses on uptime monitoring, security patches, and user support processes.
Financial services, logistics providers, and healthcare organizations use similar layered approaches. Whether managing a call center launch or implementing a new hospital procedure, starting with a flexible prototype phase, validating with a trial run, and then sustaining with a repeatable plan reduces surprises and maintains trust.
Integrating Control Plans into Daily Operations
A control plan loses value if it lives solely in a binder. Real impact comes when teams refer to it often and treat it as a guide for everyday decisions.
Here are some practical tips to weave your plan into daily work:
Train Everyone Involved
Operators, supervisors, and engineers should all understand the purpose of the plan and how to use it. Simple training sessions, work instructions tied to the control plan, and visible charts near workstations reinforce its importance.
Visual Controls
Where possible, translate parts of the plan into visual standards: charts, dashboards, or color-coded gauges. Visual cues help teams spot trends and take action faster.
Audits and Layered Process Checks
Regular checks ensure the plan remains accurate and operators follow it. Layered audits, where different levels of management review process adherence, create accountability and encourage continuous improvement.
Keep It Dynamic
A control plan shouldn’t remain static. Whenever you introduce a process change, equipment upgrade, or new design feature, revisit the plan. This keeps it relevant and ensures controls evolve alongside your operations.
Common Pitfalls to Avoid
While the benefits of a control plan are clear, several pitfalls can undermine its effectiveness. Here are a few to watch out for:
Treating It as a One-Time Project
Some organizations see the control plan as a task to complete before a customer audit, then shelve it. Instead, treat it as a living document that evolves with your process.
Lack of Operator Involvement
Operators often have deep insights into what goes wrong in a process. Engage them when developing or updating the plan to uncover practical issues and workable solutions.
Overcomplicating It
Detail is good, but information overload can overwhelm frontline teams. Balance precision with usability. If a control plan is too complex to follow, it may end up ignored.
Bringing It All Together
Building a robust control plan takes effort, cross-functional collaboration, and a commitment to detail. When done well, it becomes a vital part of your quality assurance strategy, catching problems before they reach your customers.
Start by revisiting your current control plans. Do they reflect your actual process? Are critical characteristics up to date? Do operators rely on them daily? If gaps exist, gather your team and refine the plan together.
In the end, the goal is simple: deliver consistent results that delight customers, protect your brand, and make daily work more predictable. A solid control plan provides the road map for getting there, one process step at a time.