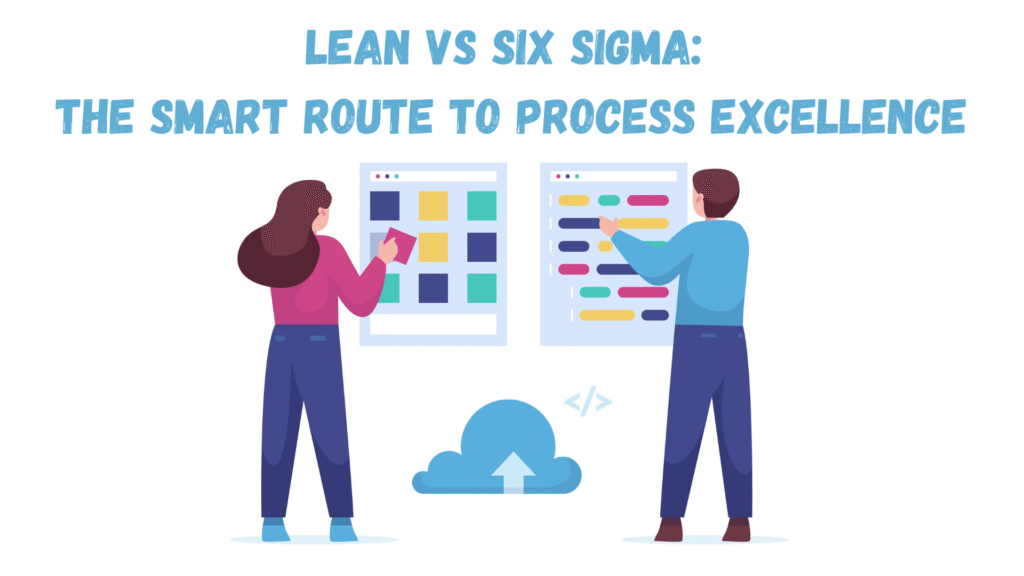
Lean vs Six Sigma: The Smart Route to Process Excellence
Picture a production manager walking a busy shop floor in 2025. Digital dashboards broadcast takt time, defect parts per million, and on-time delivery. A belt of autonomous vehicles moves material with almost choreographed grace. Yet profit targets feel just out of reach. The team wonders which improvement playbook delivers the bigger leap—Lean or Six Sigma. That single question sparks an important conversation about focus, tools, data depth, and culture.
Why Efficiency Remains the Ultimate Competitive Edge
Global supply networks and real-time customer expectations leave little tolerance for waste or fluctuation. Shaving hours from throughput or cutting defects by a single sigma still converts directly to cash, even in a world filled with advanced analytics and robotics.
Lean Thinking: Flow at the Speed of Customer Demand
Lean traces its roots to Toyota’s post-war pursuit of “ideal flow.” Over decades that philosophy crystallized into five guiding principles—value definition, value-stream mapping, uninterrupted flow, just-in-time pull, and relentless perfection. Practitioners hunt eight categories of waste—transport, inventory, motion, waiting, over-production, over-processing, defects, and untapped talent.
Popular Lean tools
- Value-stream maps highlight queues and unbalanced workloads
- Kaizen events deliver concentrated bursts of improvement
- 5S brings visual order that reduces search time and hazard
- Heijunka (level loading) aligns production rhythm with demand
Lean favors short cycles, visible metrics, and employee involvement. A team can redesign a cell in a week and watch lead time fall by half. Statistical depth remains light; decisions often rely on direct observation and tactile experiments. This strength makes Lean adaptable across healthcare, banking, and even software sprints where rapid cycles matter more than deep data.
Six Sigma: Variation Control Through Data Discipline
Six Sigma emerged at Motorola during the late 1980s, propelled by Bill Smith’s realization that hidden variability drained warranty cost more than obvious scrap. The method aims for 3.4 defects per million opportunities—roughly six standard deviations between the process mean and the nearest spec limit.
Core elements
- DMAIC roadmap: Define, Measure, Analyze, Improve, Control
- Roles and belts: Green Belts pursue part-time projects; Black Belts spend full time; Master Black Belts coach strategy
- Statistical arsenal: hypotheses tests, regression, ANOVA, design of experiments, control charts
Six Sigma projects generally focus on chronic quality pain or cost erosion where root causes hide inside noise and complex interactions. Because the method leans on data integrity and statistical power, projects run longer—often four to six months—and require rigorous project charters.
A Head-to-Head Comparison
Criterion | Lean Focus | Six Sigma Focus |
Primary Goal | Speed and waste removal | Stability and defect elimination |
Typical Horizon | Days to weeks | Months |
Data Intensity | Visual cues, simple metrics | Statistical models |
Change Agent | Cross-functional teams | Belt-certified analysts |
Culture Signal | Everyday Kaizen | Structured project cadence |
A blended perspective reveals complement rather than competition. Lean shortens loops and exposes variation faster. Six Sigma quantifies that variation and locks gains through statistical control.
When Lean Shines Brightest
- High-mix, low-volume cells: Frequent changeovers amplify waiting and motion. Quick setup (SMED), flexible staffing, and visual scheduling collapse idle time
- Service touchpoints: Emergency departments, insurance claims, and call centers reward real-time flow over deep statistical sampling
- Early digital transformations: Firms beginning their Industry 4.0 journey often see hidden queues once data becomes transparent. Lean offers immediate traction by trimming surfaces before analytics scale up
Case example: A food processing plant mapped its pasta line and discovered pallets traveling 1.8 kilometers between forming and packaging. A single-day spaghetti flow workshop relocated equipment, which cut travel distance to 300 meters and trimmed eight hours of inventory.
When Six Sigma Delivers Breakthroughs
- Regulated environments: Aerospace, medical devices, and pharmaceuticals demand validated, evidence-backed defect prevention
- Cost of poor quality (COPQ) above five percent of sales: Deep analysis often uncovers chronic variation hidden behind rework buffers
- Data-rich processes: Semiconductor fabs, fintech transaction engines, or telecommunication networks generate granular logs ideal for ANOVA, logistic regression, and advanced control charts
Case example: A global credit-card processor flagged sporadic authorization delays above 800 milliseconds. A DMAIC team applied multi-factor DOE on server configurations and cut latency spread to under 300 milliseconds, freeing bandwidth for peak holiday volume.
Lean Six Sigma: Better Together
Digital operations in 2025 rarely pick a single banner. Instead, organizations design a hybrid approach—Lean paves flow for quick wins, Six Sigma locks capability, while Industry 4.0 technology captures streaming data. Recent research highlights how Lean Six Sigma combined with Industrial IoT predicts failure modes and lowers maintenance cost by 25 percent.
Integration blueprint
- Start with a value stream scan: Amplify process-wide visibility
- Layer DMAIC on priority choke points: Allow data breakthroughs to cascade through Lean flow
- Digitize control plans: Sensors flag drift instantly; automated alerts guide rapid response
- Coach fusion roles: “Digital Green Belts” learn Python, Power BI, and time-series modeling
Governance and Deployment in 2025
- Executive steering cadence: Monthly portfolio reviews rank projects by value creation, risk, and people development
- Skill paths: Yellow Belts for foundational awareness; Digital Green Belts for Python-driven statistics; Black Belts for enterprise cross-function challenges
- Digital obeya rooms: Large interactive walls broadcast value-stream maps, sigma levels, and real-time OEE
- Citizen analytics: Low-code platforms allow front-line teams to build dashboards, closing information loops within a single shift
Measuring Success
Metric | Lean Lens | Six Sigma Lens |
Lead Time | Median hours per part | Same, plus variance coefficient |
Scrap | First-pass yield | Defects per million opportunities |
Cash Impact | Inventory turns | Cost of poor quality |
Agility | Plan-versus-actual takt adherence | Process capability index (Cpk) |
Balanced scorecards nudge leadership toward joint objectives—speed, stability, and sustainable margins.
Conclusion: Choosing Wisely Then Blending Boldly
Lean favors action and visual flow. Six Sigma excels at rooting out subtle variation through disciplined analytics. Leaders who master both gain a dual advantage—quick payback and sustained defect control. As connected sensors and AI turbo-charge data volume, Lean Six Sigma offers a proven framework that clarifies signal from noise while keeping people at the center of improvement.
Step onto your own shop floor, digital workspace, or clinic hallway today. Map the flow, gather the data, engage your talent, and write the next chapter of process excellence—one smart decision at a time.