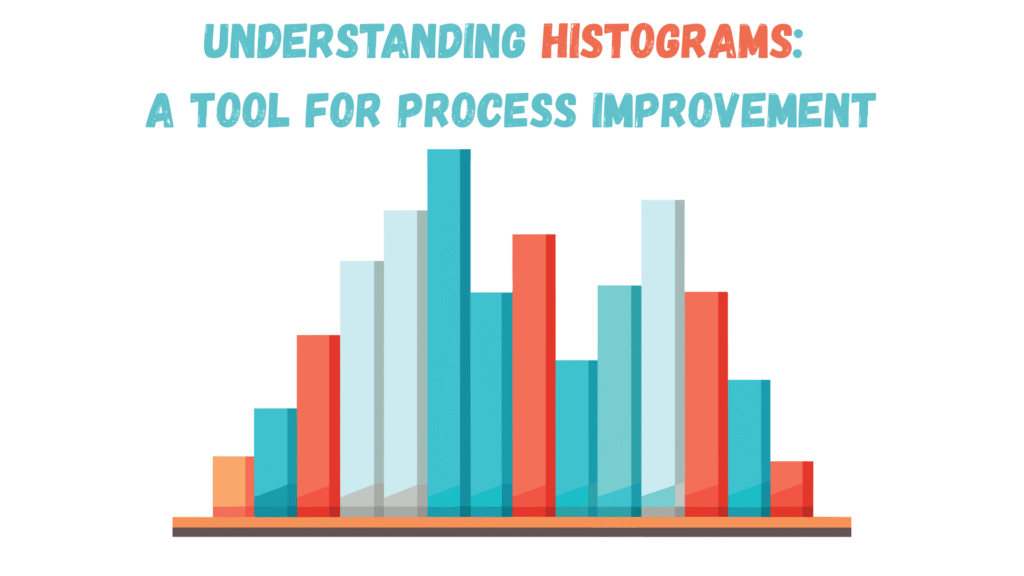
When was the last time you looked at a pile of data and thought, “Where do I even begin?” Raw numbers by themselves rarely tell the whole story. They need a translator — and that’s where the humble histogram steps in. A histogram may look like a simple bar chart at first glance, yet its power in revealing patterns and process variations makes it a trusted companion for quality professionals, Six Sigma practitioners, and continuous improvement champions across industries.
In this detailed guide, you’ll learn how histograms work, why they matter, and how you can harness them to spot trends, solve problems, and drive real process improvements.
What is a Histogram, Really?
A histogram is a type of bar graph that displays the distribution of numerical data. Unlike a regular bar chart, which shows categories, a histogram groups data into ranges called bins. Each bar represents how many data points fall within that range.
Think of measuring the weight of 100 metal rods produced in a factory. Instead of listing each rod’s weight, a histogram shows how many rods weigh between, say, 9.5 to 10 grams, 10 to 10.5 grams, and so on. This simple visual instantly shows you whether your production is consistent or if variations exist that need attention.
The Origins and Enduring Power of the Histogram
The concept of the histogram can be traced back to the 19th century, but it was the quality revolution of the 20th century that made it a staple tool. W. Edwards Deming, Kaoru Ishikawa, and other pioneers embedded histograms into the everyday toolkit of Total Quality Management. Ishikawa, for instance, listed the histogram as one of the “Seven Basic Quality Tools,” a proof of its value in practical problem-solving.
So, why does it still matter today? Because processes still generate variation, and leaders still need to understand and control it. A histogram cuts through the noise and lays bare the truth hidden in numbers.
Why Use a Histogram Instead of a Simple Average?
Averages can be misleading. Imagine two machines producing bolts. Both have an average length of 5 cm. Sounds good, right? But what if Machine A’s lengths cluster tightly around 5 cm, while Machine B swings wildly between 4.5 cm and 5.5 cm? That’s a problem.
A histogram brings this variation to light. While the average is just one figure, the histogram shows the entire spread — revealing whether you have consistent performance or hidden outliers that could cause defects or rework.
When Should You Use a Histogram?
Histograms are versatile, but they truly shine in specific scenarios:
- Understanding Process Behavior: Are you seeing natural variation or something unusual that needs investigation?
- Comparing to Specifications: Do your data points fall inside customer specifications or acceptable limits?
- Monitoring Process Changes: Did your recent process tweak reduce variation or introduce new problems?
- Root Cause Analysis: Where should you dig deeper if a process is underperforming?
Whether you’re analyzing cycle time, defect counts, delivery delays, or energy usage, histograms reveal patterns that might otherwise stay hidden in a spreadsheet.
How to Build a Meaningful Histogram
Building a histogram may seem straightforward, yet the quality of your output depends heavily on the thought you put in before you ever draw that first bar. Let’s unpack each step in more detail so you can move from a basic chart to a reliable visual that genuinely drives action.
1. Collect Sufficient and Reliable Data
Begin by asking yourself: what question am I trying to answer? This question will guide what data you collect and how much you need. For example, if you want to understand daily production output variation over a month, one week of data might give you only a partial picture.
Consistency matters too. If measurements come from different shifts, machines, or operators, note those factors. You may uncover hidden subgroups that explain variation. Always ensure your measurement system is calibrated and repeatable so your histogram reflects reality rather than measurement errors.
2. Choose Bins Thoughtfully
The decision on how to group data, i.e., your bins, shapes what your histogram reveals. There is no universal rule, but there are practical guidelines.
Start by calculating the range: subtract the smallest data point from the largest. Next, decide how many bins make sense.
Use your judgment to test multiple bin sizes and see which pattern best represents the data’s natural behavior. If you switch to a smaller bin width and your histogram changes dramatically, you might not have enough data yet.
3. Count and Tally Accurately
Once bins are defined, count how many data points fall into each bin. For larger data sets, spreadsheets or statistical software handle this well, but even when automated, verify your results with a quick manual check of a few values. Errors in the frequency count can distort your entire picture.
Keep your counts organized in a table that you can revisit later if your analysis needs to change. Recording counts this way also makes your work transparent if you’re presenting it to stakeholders.
4. Plot with Clear Design
When you plot your histogram, clarity is everything. Draw your horizontal axis to show bins in ascending order, whether they represent time, measurements, or any other continuous variable.
The vertical axis should display the frequency for each bin. Each bar should be touching its neighbor because the data represents continuous ranges, not separate categories. This small detail distinguishes histograms from bar charts and reinforces the message that the data flows from one bin to the next.
Label both axes clearly, use consistent units, and always add a title that explains what the histogram represents. A histogram buried in a slide deck with vague labeling can cause more confusion than insight.
5. Add Meaningful Context
Numbers become powerful when you connect them to expectations or standards. Consider layering in:
- Target values: Where you want the data to center.
- Specification limits: Upper and lower thresholds your process must stay within.
- Historical comparisons: If you’ve run similar histograms in the past, how does today’s process measure up?
These contextual elements help people who review your histogram quickly see whether the process is stable, capable, or trending toward an issue.
Reading a Histogram: What to Look For
Once you have your histogram, what story does it tell? Here are some common shapes and what they often suggest:
Normal (Bell-Shaped)
This classic shape indicates that most data points cluster around the center. Many manufacturing and service processes aim for this predictable distribution.
Skewed Right (Positively Skewed)
A tail stretching to the right suggests that a few larger values pull the mean upward. This might hint at occasional large delays or higher-than-expected defect counts.
Skewed Left (Negatively Skewed)
A tail on the left means smaller values occur less frequently. Depending on context, this could reveal underutilization or early completions.
Bimodal (Two Peaks)
Two peaks often suggest that two different processes or shifts are at play. For example, two machines with different calibrations or two teams using different methods.
Outliers
Bars that sit far from the rest indicate anomalies. One or two outliers may warrant investigation for special causes.
Avoiding Common Pitfalls
While histograms are simple, they can mislead if used poorly. Watch for these traps:
- Inappropriate Bins: Choosing bins without considering data range can hide or exaggerate trends. Always experiment with bin sizes to see what reveals the true story.
- Insufficient Data: Too few points may show random noise rather than real patterns. Make sure your sample size is meaningful.
- Ignoring Context: A histogram shows what’s happening, but understanding why demands process knowledge and deeper analysis.
Histograms as a Gateway to Deeper Analysis
A histogram often sparks further questions. It might reveal that your process is stable but off target, or unstable with unpredictable results. Either way, it sets the stage for other tools:
- Control Charts: To monitor process stability over time.
- Pareto Charts: To rank categories of problems.
- Cause-and-Effect Diagrams: To explore root causes of variation.
When used together, these tools form a powerful toolkit for continuous improvement.
Bringing Histograms Into Everyday Practice
Creating a histogram is not the goal, improving the process is. Leaders and teams who build a culture around data visualization develop sharper instincts for solving problems before they escalate. Histograms become a regular part of daily stand-ups, monthly reviews, or strategic decision-making.
In many Lean and Six Sigma projects, a histogram often appears in the “Measure” phase of DMAIC. It validates the baseline performance and later shows whether improvements hold up. It also builds credibility: when you show a clear, visual distribution, you win support faster than with a spreadsheet full of numbers.
Tips to Maximize the Value of Histograms
- Keep them visible: Post them on team boards or dashboards.
- Make them understandable: Use clear labels, meaningful bin sizes, and plain explanations.
- Connect them to action: Use the insights to guide changes, not just to display information.
- Combine with storytelling: Numbers come alive when you explain what they mean for customers, costs, and quality.
The Takeaway: See Beyond the Numbers
A histogram turns raw data into a visual narrative. It helps you see patterns you might miss otherwise. It uncovers the voice of the process, telling you when things are stable and when they need your attention.
In the end, process improvement is about seeing reality clearly, acting with purpose, and sustaining gains over time. The histogram stands as one of the simplest yet most reliable guides on that journey.
So next time you wonder where your process stands, remember: before you jump to conclusions or spend weeks chasing root causes, let the data speak through a histogram. You might find the trends and the improvements waiting right there in plain sight.