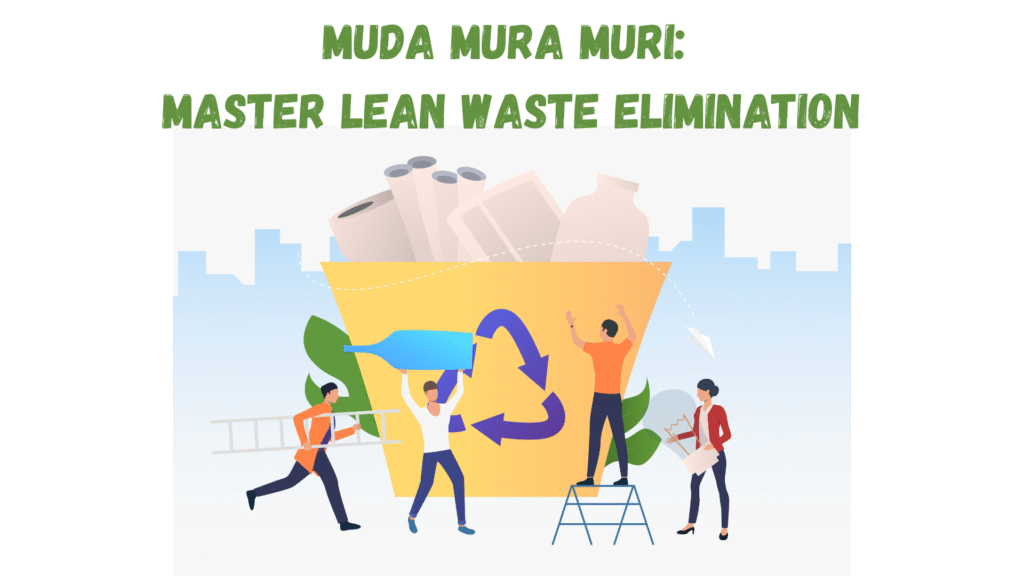
Muda Mura Muri: Master Lean Waste Elimination
Ever feel like your team is running at full speed yet work keeps piling up, costs keep rising, and problems keep repeating? You’re not alone. Many organizations get stuck fighting the same fires every day. The good news is, there’s a clear path out of this cycle and it starts with three simple Japanese words: Muda, Mura, and Muri.
These terms form the backbone of the Toyota Production System and modern Lean thinking. They help us see where waste hides, where work becomes uneven, and where people and machines get pushed too far. The goal? A workplace where processes flow smoothly, teams work sustainably, and customers get better value, all without needless cost or stress.
In this guide, you’ll learn where Muda, Mura, and Muri come from, how they’re connected, and how you can tackle them step by step. By the end, you’ll see your work through a Lean lens that exposes what holds you back and you’ll have practical ideas to fix it.
The Origins of Muda, Mura, and Muri
These three concepts come from the Toyota Production System (TPS), developed in post-war Japan. Leaders like Taiichi Ohno and Shigeo Shingo realized that just focusing on cutting visible waste was never enough. When they dug deeper, they found that hidden causes like imbalance and overburden were just as damaging, if not more.
TPS inspired the Lean movement worldwide. The idea was revolutionary: instead of producing as much as possible, produce exactly what customers want, when they want it, with minimal waste and maximum respect for people.
What makes Muda, Mura, and Muri so powerful is that they work together. If you only fight one, you risk letting the others creep in and undo your efforts. That’s why the best Lean organizations make them part of daily problem-solving.
Muda: Spotting the Obvious Waste
Let’s start with the waste that jumps out first — Muda. This word means “wastefulness” or “uselessness.” In Lean, Muda is any activity that uses time, money, or effort yet creates no value for the customer.
Taiichi Ohno famously identified seven types of Muda, later expanded to eight. They help you break down your processes and ask, “Does this step add value, or is it just eating up resources?”
The 8 Wastes Explained with Real-World Examples
- Overproduction
Imagine a bakery making 500 croissants for the day when sales usually reach 200. The extras go stale, costing ingredients and storage. - Waiting
In an office, waiting happens when employees can’t proceed because they’re stuck for an approval. Valuable skills sit idle. - Transport
Moving goods more than needed like a hospital moving medical files between floors multiple times a day instead of digitizing them. - Extra Processing
Think of customer reports filled with data nobody reads. The effort adds no real value. - Inventory
Stockpiling supplies ties up money that could be invested elsewhere. Too much inventory also hides defects that only appear when items finally get used. - Motion
Searching for tools in a disorganized maintenance shop. All that bending, walking, and looking adds up to lost time. - Defects
A car recall because of a faulty part means repairs, reputational damage, and customer frustration. - Underutilized Talent
An overlooked form of waste. When companies ignore frontline workers’ ideas for improvement, valuable insight goes untapped.
Spotting Muda is a good first step. But the real power of Lean shows up when you ask: what created this waste in the first place?
Mura: The Hidden Unevenness
Mura translates to “unevenness” or “inconsistency.” While Muda is visible, Mura often stays in the shadows until it causes bigger problems.
Picture a call center. On Mondays, calls pour in and staff scramble. On Fridays, the same team sits idle. This uneven work creates chaos during peaks and wasted resources during lows.
Unevenness can come from:
- Poor planning or forecasting
- Unpredictable demand
- Inconsistent work standards
Even highly motivated teams get exhausted if their workload swings between extremes. Customers feel the impact too with missed deadlines or poor service during high-stress times.
The fix? Level the flow of work so teams can handle it steadily. It might mean better scheduling, more accurate demand forecasting, or designing processes that adjust easily.
Muri: The Damage of Overburden
Muri means “overburden” or “unreasonable stress.” It shows up when people or machines run beyond their natural limits for too long.
When people are pushed too hard, mistakes happen. Absenteeism rises. Good employees burn out or leave. When machines are pushed too hard, they break down more often and require costly repairs.
Here’s an example: a delivery company schedules drivers to complete routes that take 11 hours when the legal driving limit is 8. Drivers rush, skip breaks, and risk accidents. The company saves nothing because any short-term gain is lost to errors, repairs, or legal issues.
Many leaders miss Muri because they see pushing people harder as a way to get more done. In Lean, the opposite is true: steady, reasonable workloads produce better results over time.
How Muda, Mura, and Muri Work Together
One of the biggest mistakes companies make is treating these three as separate problems. They feed off each other.
Imagine an e-commerce warehouse:
- Orders spike every Friday (Mura).
- Staff rush orders out the door to meet tight delivery promises, skipping checks (Muri).
- Wrong items get shipped, and products get damaged in the rush (Muda).
If the company tries to fix waste (Muda) without addressing the root imbalance (Mura) or the excessive strain (Muri), the problems return every week. Lean thinkers understand this cycle and focus on all three together.
Practical Steps to Eliminate Muda, Mura, and Muri
Talking about the three Ms is useful, but real impact comes from action. Here are clear, practical ways you can tackle them, whether you lead a factory, office, hospital, or tech startup.
1. Map Your Value Stream
A Value Stream Map (VSM) is your blueprint for improvement. It shows each step needed to deliver a product or service, and how information flows.
Here’s how to get started:
- Gather a cross-functional team, people who do the work, not just managers.
- Map the current state. Include every handoff, wait time, and rework loop.
- Mark areas where waste shows up: idle time, piles of unfinished work, or repeated tasks.
- Identify the root causes: is it due to uneven demand, unclear roles, or overworked people?
This process often reveals surprising connections between Muda, Mura, and Muri.
2. Level the Workload (Heijunka)
Unevenness (Mura) often comes from unpredictable schedules. Lean uses Heijunka, a method of leveling production. It doesn’t mean demand must be constant; it means the process can handle variation without stress.
For example:
- In retail, spread out promotions instead of creating massive spikes.
- In a software team, balance feature releases so developers aren’t slammed one sprint and idle the next.
- In healthcare, use appointment slots to reduce waiting room peaks.
Leveling reduces overburden and hidden waste that comes from firefighting.
3. Standardize Work
Standardized work is about creating best practices so everyone follows the most efficient method. It cuts out variation that feeds Mura and Muda.
Good standardization is flexible:
- Clear steps for tasks that repeat often.
- Visual work aids — photos, diagrams, checklists.
- Input from frontline teams to refine and improve standards.
Standardized work frees people to innovate instead of reinventing the wheel each time.
4. Build Quality Into the Process (Jidoka)
Lean encourages building quality at the source. Jidoka gives workers the authority to stop work if they spot a problem. This avoids passing defects downstream.
Examples include:
- An assembly line with an Andon cord workers pull when they see a defect.
- An accounting team with clear checkpoints to catch errors early.
- A software pipeline that runs automated tests before pushing updates live.
Preventing mistakes early reduces costly rework later.
5. Use Visual Management
Visual tools make it easy for everyone to see where work stands. Kanban boards, dashboards, color coding, and signals reveal hidden waste, imbalance, and overburden.
Visual management helps:
- Spot when tasks pile up.
- Show who needs help.
- Reveal bottlenecks before they become crises.
One example is a hospital using color-coded patient flow boards to balance staff loads across wards.
6. Foster a Culture of Kaizen
Kaizen means continuous improvement. Small, daily changes keep waste from creeping back. Leaders who encourage Kaizen build trust. People feel safe speaking up when they see ways to improve.
Ways to foster Kaizen:
- Hold short, regular huddles for teams to share ideas.
- Act on suggestions quickly.
- Celebrate small wins, not just big projects.
When improvement becomes everyone’s job, Muda, Mura, and Muri shrink naturally.
Building a Truly Lean Organization
Tackling Muda, Mura, and Muri is about more than saving money. It’s about building an organization that runs smoothly, adapts easily, and respects people.
- Customers get consistent, high-quality service.
- Employees stay engaged and less stressed.
- Leaders spend less time firefighting and more time creating value.
Remember: real Lean success is never a one-time fix. It’s a daily habit. Look for waste, see where work gets uneven, and watch for signs of overburden. Encourage your teams to spot issues early and take action together.
Final Thoughts
Next time you hear someone say “Lean is just about cutting waste,” you’ll know better. Muda, Mura, and Muri form a system. They connect, overlap, and feed each other. Address them together and you build processes that stand the test of time.
So, walk your workplace, map your flows, talk to your people. Waste hides in plain sight. Imbalance lurks behind the numbers. Overburden wears down your best people and tools. But once you see it, you can fix it and that’s how you become truly Lean.