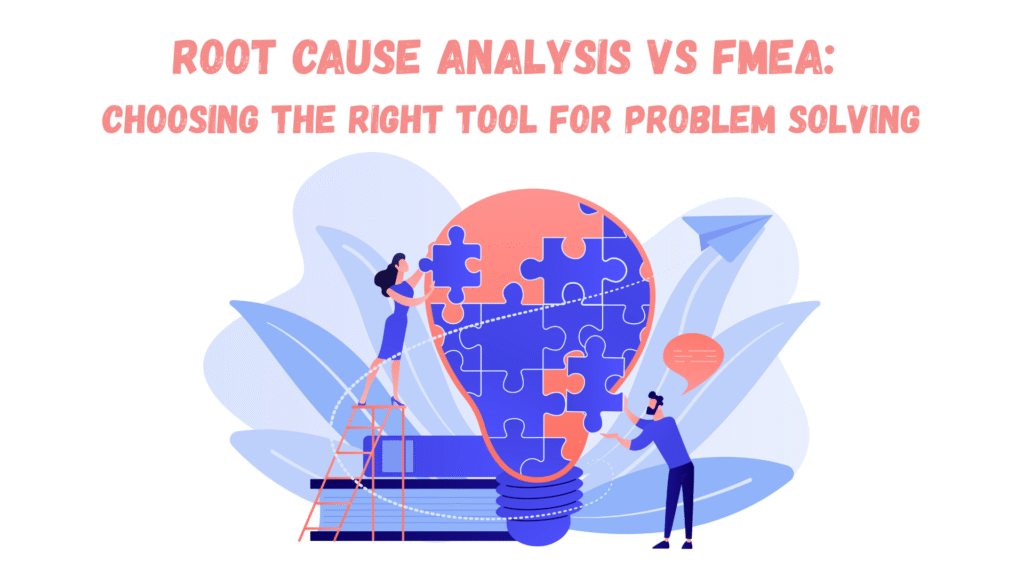
Root Cause Analysis vs FMEA: Choosing the Right Tool for Problem Solving
When issues arise in operations, manufacturing, or product design, organizations rely on structured methods to address them effectively. Among the most widely used techniques are Root Cause Analysis (RCA) and Failure Modes and Effects Analysis (FMEA). Although both are essential to quality and risk management, they serve different purposes, follow different logic, and are best suited to different stages of a problem’s lifecycle.
In this blog, we’ll explore RCA and FMEA in depth, what each method is, how it works, their similarities and differences, and most importantly, how to decide which method to use based on the problem at hand. Whether you’re an engineer, quality professional, or process owner, understanding these tools will enhance your decision-making and improve long-term reliability.
What is Root Cause Analysis (RCA)?
Root Cause Analysis is a reactive method used to identify the underlying causes of a problem that has already occurred. Its primary objective is not to fix the symptom but to address the source of the issue to prevent recurrence. RCA focuses on understanding what happened, why it happened, and how to prevent it from happening again.
Key Principles of RCA
- Problem-Centric: RCA begins with a specific issue, an event, defect, or failure that has already taken place.
- Systematic Investigation: The process involves structured tools like the 5 Whys, Fishbone Diagram (Ishikawa), or Fault Tree Analysis.
- Focus on Cause, Not Blame: It aims to explore processes and systems rather than assign fault to individuals.
- Permanent Corrective Action: The end goal is a sustainable fix that addresses the root causes and prevents recurrence.
Common Use Cases
- Unexpected machine breakdowns in manufacturing
- Defects reported from the customer end
- Safety incidents in production environments
- Service failures in IT or support processes
What is FMEA (Failure Modes and Effects Analysis)?
Failure Modes and Effects Analysis is a proactive technique used to anticipate what could go wrong in a process, product, or system. It focuses on identifying potential failure modes before they occur and evaluating their impact, cause, and likelihood. Based on this, teams can prioritize risks and take preventive measures early in the design or operational phase.
Key Principles of FMEA
- Risk-Focused: FMEA is built around evaluating risk by calculating Risk Priority Numbers (RPN) based on severity, occurrence, and detection.
- Forward-Looking: It helps predict and mitigate potential problems before they lead to actual failures.
- Team-Based: FMEA often involves cross-functional collaboration, especially during design or process development.
- Prioritization of Action: By quantifying risk, FMEA guides teams on which potential failures to address first.
Common Use Cases
- Designing a new product or service
- Developing or changing a manufacturing process
- Enhancing a complex system involving multiple variables
- Conducting safety or compliance reviews
RCA vs. FMEA: Core Differences
While both RCA and FMEA are problem-solving tools, their purpose, timing, approach, and mindset differ significantly.
Feature | Root Cause Analysis | FMEA |
Timing | After a problem occurs | Before a problem occurs |
Focus | Actual failures | Potential failures |
Goal | Eliminate root causes | Reduce risk likelihood |
Approach | Investigative and diagnostic | Preventive and predictive |
Tools Used | 5 Whys, Fishbone Diagram, Fault Tree | RPN matrix, Process Flow Diagrams |
Data Requirements | Evidence from a known failure | Process knowledge, historical data |
Outcome | Permanent corrective actions | Preventive actions and design improvements |
Understanding these differences is crucial in selecting the right method based on your situation. RCA aims to stop recurring issues by addressing the root cause, while FMEA seeks to avoid future problems by addressing potential weak spots.
When to Use Root Cause Analysis
RCA is ideal when a failure or problem has already occurred and needs to be understood thoroughly to avoid repetition. It is not concerned with hypothetical risks but actual outcomes that have created loss, downtime, or customer dissatisfaction.
Example Scenario:
A manufacturing line experiences repeated shutdowns due to a packaging defect. RCA helps dissect this issue by identifying whether the defect originates from the sealing equipment, material inconsistency, or human error. The team traces the root cause, discovers a misaligned sensor, and installs a new calibration protocol.
In this case, applying RCA provides insight into a single event and produces a targeted, lasting fix.
When to Use FMEA
FMEA fits best during the planning, design, or early operational stages, long before a failure takes place. It is useful in evaluating how each step in a process could go wrong and what the consequences could be.
Example Scenario:
Before launching a new electronic product, the design team uses FMEA to analyze the circuit design. They identify a potential failure in the power regulation component that could cause overheating. Based on a high RPN score, they redesign the component layout to improve cooling and add detection sensors to alert users.
Here, FMEA acts as a shield against future quality issues, recalls, and safety risks.
Can RCA and FMEA Be Used Together?
Absolutely. RCA and FMEA are complementary methods. In fact, high-performing organizations often apply both techniques as part of a continuous improvement loop.
Example Integration:
- Use FMEA First: During product development, run FMEA to predict and mitigate high-risk failure modes.
- Use RCA Later: If a failure still occurs post-launch despite FMEA efforts, conduct RCA to investigate the missed gap.
- Update FMEA Based on RCA: Feed the findings from RCA back into the FMEA to update risk scores and controls.
This integrated approach creates a feedback loop where learning from real-world failures enhances future risk prediction.
Strengths and Limitations
Root Cause Analysis
Strengths:
- Offers deep insight into specific issues
- Drives targeted, corrective action
- Builds a culture of continuous learning
Limitations:
- Reactive in nature
- Requires detailed data from the failure event
- May become subjective without structured methodology
FMEA
Strengths:
- Prevents issues proactively
- Provides a risk-based prioritization framework
- Encourages cross-functional collaboration
Limitations:
- May overlook unknown or rare failure modes
- Risk scores can become inconsistent without expert alignment
- Can be time-consuming for complex systems
These limitations highlight the importance of choosing the right method or combination of methods based on context, resources, and urgency.
Best Practices for Effective Implementation
Whether you’re applying RCA or FMEA, a few best practices can ensure the process delivers meaningful results.
For Root Cause Analysis:
- Gather clear evidence before diving into analysis
- Involve front-line staff who were close to the issue
- Use multiple tools to avoid jumping to conclusions
- Focus on system-level improvements, not just quick fixes
- Document and communicate outcomes for organizational learning
For FMEA:
- Start early during design or process planning
- Keep your team cross-functional to gain varied perspectives
- Regularly update the FMEA as processes evolve
- Validate RPN scores through historical data or testing
- Link action items directly to responsible owners and due dates
Implementing these habits strengthens your quality culture and maximizes return on problem-solving efforts.
How to Choose Between RCA and FMEA
Here’s a simplified decision guide:
- Is the issue already affecting performance, safety, or customer satisfaction?
→ Use Root Cause Analysis. - Are you evaluating a new design, process, or system for possible weaknesses?
→ Use FMEA. - Do you want to integrate learning and prevention across the lifecycle of a product or process?
→ Use both RCA and FMEA in a continuous loop.
Matching the method to the moment can significantly reduce waste, boost quality, and protect business continuity.
Final Thoughts
RCA and FMEA each serve a critical function in operational excellence. RCA helps teams learn from the past by solving real problems at their source, while FMEA looks to the future, helping prevent issues before they happen.
By understanding when and how to apply each tool, professionals can build more resilient systems, deliver better products, and foster a culture that thrives on quality, safety, and improvement. Rather than viewing RCA and FMEA as competing methods, consider them as partners in your ongoing journey toward smarter, more sustainable operations.
Ready to apply them in your next project? Choose wisely, act early, and never stop learning from both successes and setbacks.