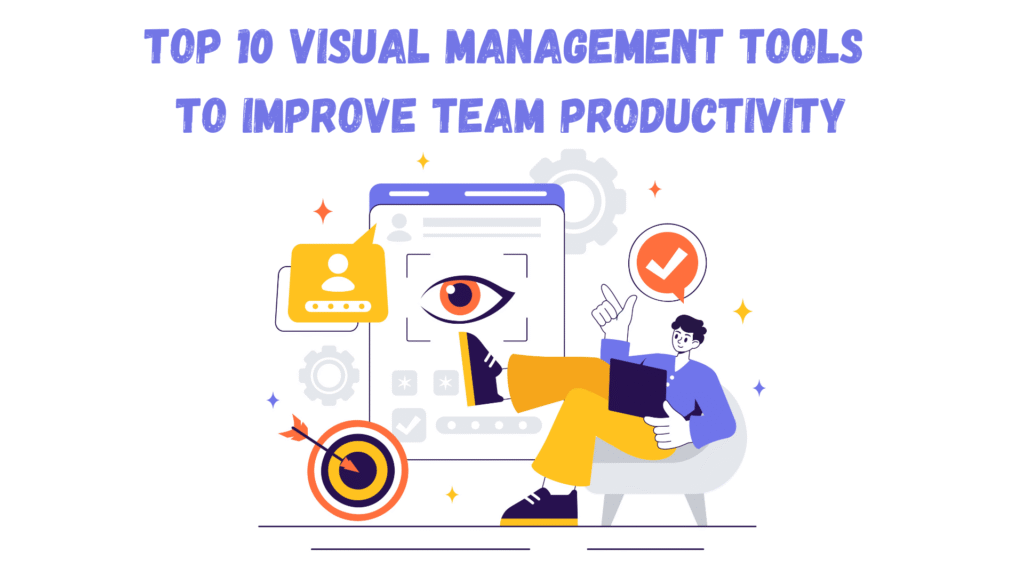
Top 10 Visual Management Tools to Improve Team Productivity
In every successful team, clarity matters. When everyone sees the same goals, understands the current status, and knows what to focus on, productivity rises naturally. That’s the power of visual management, using visual cues and systems to guide behavior, track progress, and create shared understanding.
Visual management is not a trend. It’s a practical method rooted in Lean thinking and widely applied in industries like manufacturing, software development, healthcare, logistics, and even remote teams. Whether you’re managing daily operations or long-term projects, the right visual tools can change how your team communicates, plans, and delivers.
In this blog, we’ll explore 10 of the most effective tools for visual management. These tools are more than charts and signs. Each one supports clear thinking, fast decision-making, and continuous improvement.
1. Kanban Boards
A Kanban board helps teams visualize work and limit work-in-progress. It divides tasks into columns, typically labeled “To Do,” “In Progress,” and “Done.” This structure gives a clear snapshot of the team’s workflow at any given moment.
Why it works:
- Highlights bottlenecks by showing overloaded columns
- Encourages flow by limiting how many tasks can be in progress
- Offers transparency, everyone sees the status of every task
Where to use it:
- Software development (Agile teams)
- Marketing campaign tracking
- Operations or HR task planning
Physical version: Sticky notes on a whiteboard
2. Andon Systems
Originally used in manufacturing, an Andon system uses lights or signals to alert team members when there is a problem. It ensures quick response and immediate action without verbal escalation.
Why it works:
- Encourages a fast response to issues
- Empowers frontline workers to call attention to problems
- Keeps everyone focused on quality and flow
Where to use it:
- Manufacturing assembly lines
- Customer service or call centers (real-time dashboard alerts)
- IT and DevOps environments
Modern digital Andon systems may include visual dashboards with real-time alerts, replacing traditional light systems.
3. Obeya Rooms (Big Room Planning)
Obeya means “large room” in Japanese. It’s a space where project teams gather to plan, align, and review key performance metrics. The walls are often covered with visual charts, KPIs, milestones, and problem-solving boards.
Why it works:
- Promotes cross-functional collaboration
- Keeps leadership and teams aligned with goals and metrics
- Combines short-term execution with long-term vision
Where to use it:
- Product development teams
- Strategic transformation programs
- Large-scale project coordination
Virtual Obeya rooms can be built using tools like Miro or MURAL.
4. Visual SOPs (Standard Operating Procedures)
Traditional SOPs are text-heavy. Visual SOPs use photos, flowcharts, or diagrams to show how a task should be done. This reduces training time and ensures consistency.
Why it works:
- Makes procedures easier to understand and follow
- Reduces errors and variation
- Ideal for onboarding new team members
Where to use it:
- Manufacturing and warehousing
- Service industries
- Healthcare procedures
Visual SOPs can be integrated with mobile apps or QR codes at workstations to allow instant access.
5. Huddle Boards
A huddle board is a simple, visual tool used during daily stand-up meetings or team huddles. It typically includes team goals, performance metrics, improvement ideas, and tasks.
Why it works:
- Supports daily team alignment
- Encourages engagement and ownership
- Enables real-time performance tracking
Where to use it:
- Frontline operations teams
- Healthcare units
- Agile software teams
Whether it’s a whiteboard with magnets or a digital board displayed on a monitor, the key is visibility and consistency.
6. A3 Problem Solving Boards
Named after the A3 paper size, this tool is used for structured problem-solving. It includes a visual layout for root cause analysis, countermeasures, and action plans. The format ensures that thinking stays focused, logical, and transparent.
Why it works:
- Encourages deep analysis and collaboration
- Keeps problem-solving visual and measurable
- Tracks progress with built-in accountability
Where to use it:
- Continuous improvement teams
- Quality management
- Any team using Lean or Six Sigma
Most A3 boards follow the PDCA (Plan-Do-Check-Act) cycle, which supports iterative improvement.
7. KPI Dashboards
KPI dashboards display key metrics in real time. They use charts, dials, or color-coded indicators to show performance at a glance. Whether physical (posted on walls) or digital (projected on screens), these dashboards keep the team aligned with their targets.
Why it works:
- Makes performance visible and actionable
- Encourages timely decisions and corrections
- Links daily work to strategic goals
Where to use it:
- Call centers
- Sales teams
- Supply chain and logistics
The most effective dashboards use a few focused metrics instead of overwhelming data.
8. Heijunka Boards (Production Leveling)
Heijunka boards are used in Lean production to level workflow and reduce variability. The board displays planned production volumes over time, ensuring even pacing and avoiding sudden spikes.
Why it works:
- Promotes consistent workload across teams
- Minimizes inventory and overproduction
- Encourages flexible scheduling
Where to use it:
- Production planning
- Job shops and batch processing environments
- Warehousing and fulfillment
Although it originated in manufacturing, the principle of load balancing applies across many team-based environments.
9. 5S Shadow Boards
5S shadow boards are physical boards where tools and equipment have designated locations, often outlined with paint or tape. This supports the 5S principles (Sort, Set in order, Shine, Standardize, Sustain) for workplace organization.
Why it works:
- Makes tools easy to find and return
- Reduces downtime due to searching
- Reinforces discipline and cleanliness
Where to use it:
- Workshops and maintenance areas
- Construction sites
- Laboratories and kitchens
Shadow boards are one of the clearest visual control tools. Everything has a place, and it’s immediately obvious when something is missing.
10. Color-Coded Labels and Floor Markings
These are the most basic but powerful visual controls. Labels, lines, arrows, and zones marked with colors help direct movement, indicate storage areas, and guide safety protocols.
Why it works:
- Guides behavior through visual cues
- Increases safety and compliance
- Makes layouts intuitive and self-explanatory
Where to use it:
- Warehouses and loading docks
- Hospitals and labs
- Event spaces and large offices
The key is consistency. For example, blue might mark pedestrian walkways while red could signal emergency access.
Integrating Visual Management Across the Team
Introducing visual management tools is not about adding decoration to a workspace. It’s about shaping behavior through visibility. Here’s how to make it effective:
1. Start with Purpose
Each visual tool must serve a goal, faster communication, improved flow, higher quality, or safer operations. Choose tools based on specific team challenges.
2. Make It Team-Owned
Visual systems work best when teams create and maintain them. This builds accountability and encourages daily interaction.
3. Update in Real Time
Outdated visuals lose their power. Boards, dashboards, and cues should reflect the current state of work, not last week’s status.
4. Blend Physical and Digital
Some tools work better in physical spaces. Others shine when integrated with software. The best environments combine both, adapting to where the work happens.
Conclusion: Seeing Is Empowering
When teams can see the big picture and the details at once, they act faster and smarter. Visual management says: “Let’s make the invisible visible, so we can solve problems together.”
From simple floor markings to dynamic digital dashboards, these 10 tools offer a complete spectrum of possibilities. Whether you’re building a Lean workspace or leading an Agile project, visual management can turn complexity into clarity and clarity into progress.