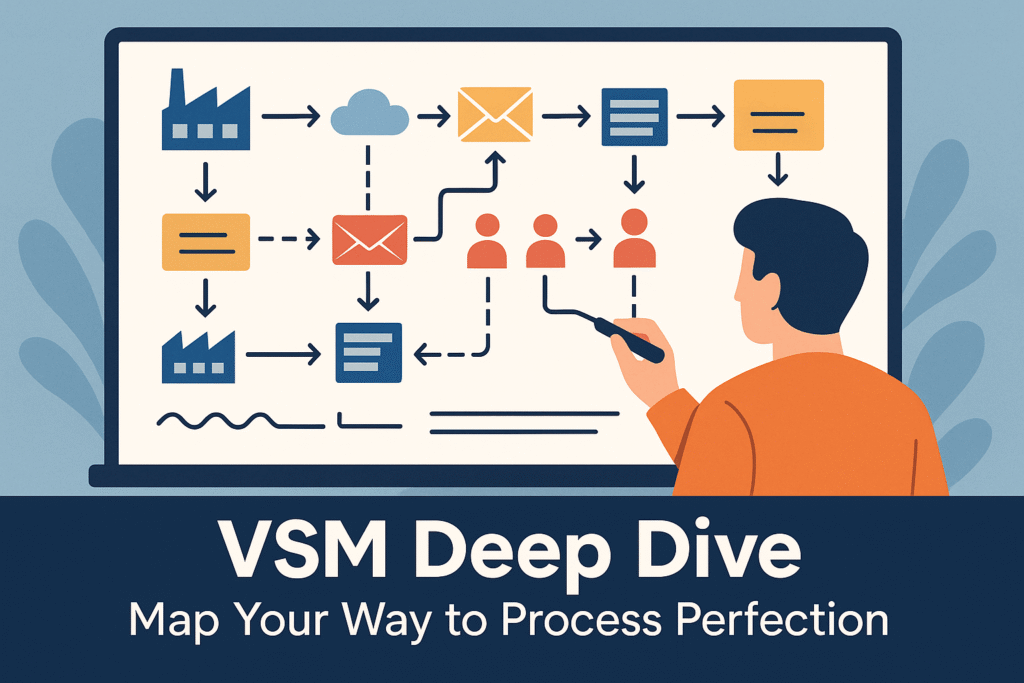
VSM Deep Dive: Map Your Way to Process Perfection
The production line was a mess. There were delay in orders, bottlenecks piled up, and no one could pinpoint the real problem. Managers blamed inefficiencies. Employees were facing frustration, and customers were growing impatient. Everyone had theories, but no clear answers.
Then, a new approach came—Value Stream Mapping (VSM). So the team gathered around a whiteboard. They mapped out every step of their process, from raw materials to final delivery. All of a sudden, the inefficiencies became obvious. It showed unnecessary handoffs, redundant approvals, and wasted motion. Within weeks, they streamlined workflows, eliminated waste, and improved delivery times.
This is the power of VSM—a structured method to visualize, analyze, and optimize any process. No matter in what sector you are manufacturing, healthcare, or service – VSM helps. So helps teams identify inefficiencies, take steps for waste reduction, and enhance productivity. In this blog, let’s explore how to create and use a Value Stream Map. You will learn how to transform complex processes into smooth, efficient operations. Let’s start.
Advanced VSM Concepts
Value Stream Mapping (VSM) is more than drawing a flowchart. It’s a powerful tool for process analysis, waste reduction, and lean implementation. So basic VSM identifies inefficiencies. But advanced VSM concepts help organizations achieve continuous improvement and operational excellence.
Key Advanced VSM Techniques
- Future State Mapping – Traditional VSM captures the current process. Yet, advanced users create a Future State Map, envisioning an optimized workflow. This allows teams to set clear improvement goals and cut bottlenecks.
- Takt Time and Load Balancing – First let us understand what Takt Time is. So it is the rate at which products must be completed to meet demand. Implementing Takt time helps with workflow synchronization. Teams can balance workloads across different stages, preventing overproduction and idle time.
- Value-Added vs. Non-Value-Added Analysis – You need to identify value-adding activities. So these are those that contribute to customer satisfaction. Further, you need to cut non-value-added tasks. So these includes delays, rework, and excess motion. So this will drive significant efficiency improvements.
- VSM for Digital & Service Industries – While originally used in manufacturing, VSM optimizes processes in various industries. This incudes IT, healthcare, finance, and logistics. Mapping information flows, software development cycles, and service delivery enhances speed and quality.
- Layered VSM & Cross-Functional Collaboration – Advanced VSM integrates many value streams. So this shows how different departments interact. This holistic view improves team collaboration, resource allocation, and end-to-end efficiency.
Why Advanced VSM Matters
Mastering Advanced Value Stream Mapping helps businesses move beyond surface-level improvements. So this helps them achieve sustainable process optimization. Through these advanced techniques, organizations can streamline workflows. Further, it can improve efficiency, and create a culture of continuous process improvement.
Is your goal refining a manufacturing line or optimizing a digital service? Then advanced VSM concepts will guide your way to process perfection.
Information Flow Mapping
Information flow mapping is a structured approach. This helps with analyzing and improving how data moves within a system. It plays a crucial role in process analysis and lean implementation. This helps with identifying inefficiencies and optimizing workflows.
One of the most effective techniques for flow mapping is value stream mapping (VSM). So this helps in visualizing the entire process from start to finish. This helps organizations understand how information flows. Further, it helps identifying where delays occur, and which areas need process improvement. By mapping out workflows, businesses can pinpoint bottlenecks. It will also identify redundant steps, and unnecessary handoffs that slow down operations.
A well-designed information flow map supports waste reduction. So how this happens? So it starts by eliminating unnecessary steps and streamlining communication between departments. It also enhances decision-making by providing a clear overview of data processing. Further, it helps by reducing errors, and improving efficiency.
Here are the key benefits of information flow mapping include:
- Leads to process improvement by identifying and eliminating waste.
- Better collaboration between teams through streamlined communication.
- Faster decision-making by reducing delays in information transfer.
- Enhanced lean implementation by aligning workflows with business goals.
Organizations looking to optimize their operations can use information flow mapping. So this acts as a strategic tool for continuous improvement. So what are the benefits of value stream mapping and process analysis? It helps businesses create lean, agile, and efficient workflows.
Material Flow Analysis
Material flow analysis helps in understanding how materials move. It tracks their movement through a production or supply chain process. Through flow mapping and process analysis, businesses can identify inefficiencies. It also helps with waste reduction and improves productivity.
One of the most effective tools for material flow analysis is value stream mapping (VSM). VSM provides visual representation of how materials move from suppliers to final products. Further, it highlights bottlenecks, delays, and areas for process improvement.
A well-structured material flow mapping approach helps organizations:
- Helps with waste reduction identifying excess inventory, transportation inefficiencies, and redundant handling.
- Improve resource use by ensuring efficient use of materials.
- Improves lean implementation by eliminating non-value-added activities.
- Streamline operations through better coordination between departments.
Time Study Integration
Time study integration is a powerful technique. This helps to measure and optimize work processes. So this ensures most efficiency and productivity. Through time study with flow mapping and process analysis, businesses can identify inefficiencies. Also it helps with reducing delays, and improve performance.
A key aspect of time study is its role in value stream mapping (VSM). So this helps to visualize the time taken for each step in a process. Through cycle times, waiting periods, and motion waste analysis, companies can pinpoint areas for process improvement and waste reduction.
A few notable benefits of time study integration include:
- Improved process efficiency by pinpointing bottlenecks and delays.
- Better resource allocation through correct measurement of task durations.
- Helps with lean implementation by minimizing non-value-added activities.
- Better workforce productivity by optimizing task processes and workflows.
Waste Identification Methods
Effective waste identification is essential for optimizing processes and improving efficiency. Value stream mapping (VSM), process analysis, and flow mapping can help businesses pinpoint waste. It will also helps them take corrective action to enhance productivity.
Common Waste Identification Methods:
Let’s understand some common methods to identify waste:
- Value Stream Mapping (VSM): This gives a visual representation of the whole process. Hence, this helps to identify delays, bottlenecks, and inefficiencies.
- The 8 Wastes of Lean: The concept comes from Lean principles. So this method categorizes waste into eight types. This includes defects, overproduction, waiting, non-utilized talent, transportation, inventory, motion, and extra processing.
- Time and Motion Studies: By analyzing the duration of each task, businesses can detect unnecessary movements. So after that, they can streamline workflows.
- Root Cause Analysis (RCA): So this is possible through the 5 Whys or Fishbone Diagram. These methods help identify the underlying causes of waste.
- Process Flow Mapping: This method visualizes every step in a process. Hence, this helps to spot redundancies and inefficiencies.
Benefits of Waste Identification:
Once businesses identify waste, it will help them with:
- Waste reduction by removing non-value-added activities.
- Process improvement through optimized workflows.
- Better lean implementation for better efficiency and cost savings.
Technology Integration
Technology integration has a great role in optimizing operations and improving efficiency. By leveraging digital tools, organizations can improve efficiency. They use value stream mapping (VSM) to analyze processes. Flow mapping helps identify bottlenecks. These methods streamline workflows and reduce waste. As a result, productivity increases. Organizations can streamline workflows, reduce waste, and enhance productivity.
Role of Technology in Lean Implementation:
Now, let’s understand how can technology help with lean implementation:
- Automated Data Collection: Real-time tracking and analytics help spot inefficiencies and improve decision-making.
- Digital Flow Mapping: Advanced software tools visualize processes. Hence, this makes it easier to find bottlenecks and optimize workflows.
- AI & Machine Learning: Predictive analytics improve forecasting, reducing overproduction and unnecessary resource allocation.
- IoT & Smart Sensors: These technologies give details about machine performance. Hence, this will help with proactive maintenance and minimizing downtime.
Benefits of Technology Integration:
So what are the benefits of technology integration? Here are a few of them:
- It leads to waste reduction by automating repetitive tasks and eliminating manual errors.
- Process improvement through data-driven insights and better accuracy.
- Lean implementation with real-time monitoring and continuous optimization.
By integrating technology businesses can create smarter, more efficient operations. So this will drive long-term success.
Implementation Roadmap
A well-structured implementation roadmap is necessary. It guides value stream mapping (VSM). Additionally, it also supports process analysis. Flow mapping benefits from it as well. This will help to drive efficiency and reduce waste. By following a clear plan, organizations can achieve process improvement. Moreover, this will lead to effective lean implementation.
Step-by-Step Implementation Roadmap:
- Assess Current Processes – Have a detailed process analysis. So this will help identify inefficiencies, bottlenecks, and waste.
- Develop a Value Stream Map – Use flow mapping to visualize workflows. Also, highlight areas for waste reduction.
- Set Improvement Goals – Define clear objectives for process optimization. So this includes cost savings, efficiency gains, and reduced lead times.
- Use Lean Strategies – You can start applying lean principles. This includes 5S, continuous improvement (Kaizen), and automation to streamline operations.
- Track and Measure Performance – You must track key metrics and adjust strategies. So this will ensure continuous improvement.
Performance Metrics
There are several key performance indicators that you should track. So this will help to measure the success of VSM, process analysis and flow mapping. By measuring key indicators, businesses can identify inefficiencies. So this will assist with waste reduction, and lead to successful lean implementation.
Some Key Performance Metrics you can track include:
- Cycle Time: Measures the time taken to complete a process from start to finish. Hence, this helps identify delays.
- Lead Time: So this tracks the total time from order placement to delivery. Hence, this will help to identify bottlenecks.
- First Pass Yield (FPY): This checks product quality by measuring the percentage of defect-free outputs.
- Overall Equipment Effectiveness (OEE): This checks machine performance based on availability, performance, and quality.
- Inventory Turnover: Indicates how well inventory management happens, reducing excess stock and waste.
- Cost of Poor Quality (COPQ): Calculates the financial impact of defects and rework.
Final Words
Value Stream Mapping (VSM) helps identifying waste, reducing inefficiency, and driving process improvement. This gives businesses visibility on possible bottlenecks, redundancies, and areas for lean implementation.
A comprehensive understanding of VSM allows businesses to fine-tune their operations. It helps boost productivity, and foster a culture of constant improvement. Moreover, VSM helps in getting practical and actionable insights into what is working for you.