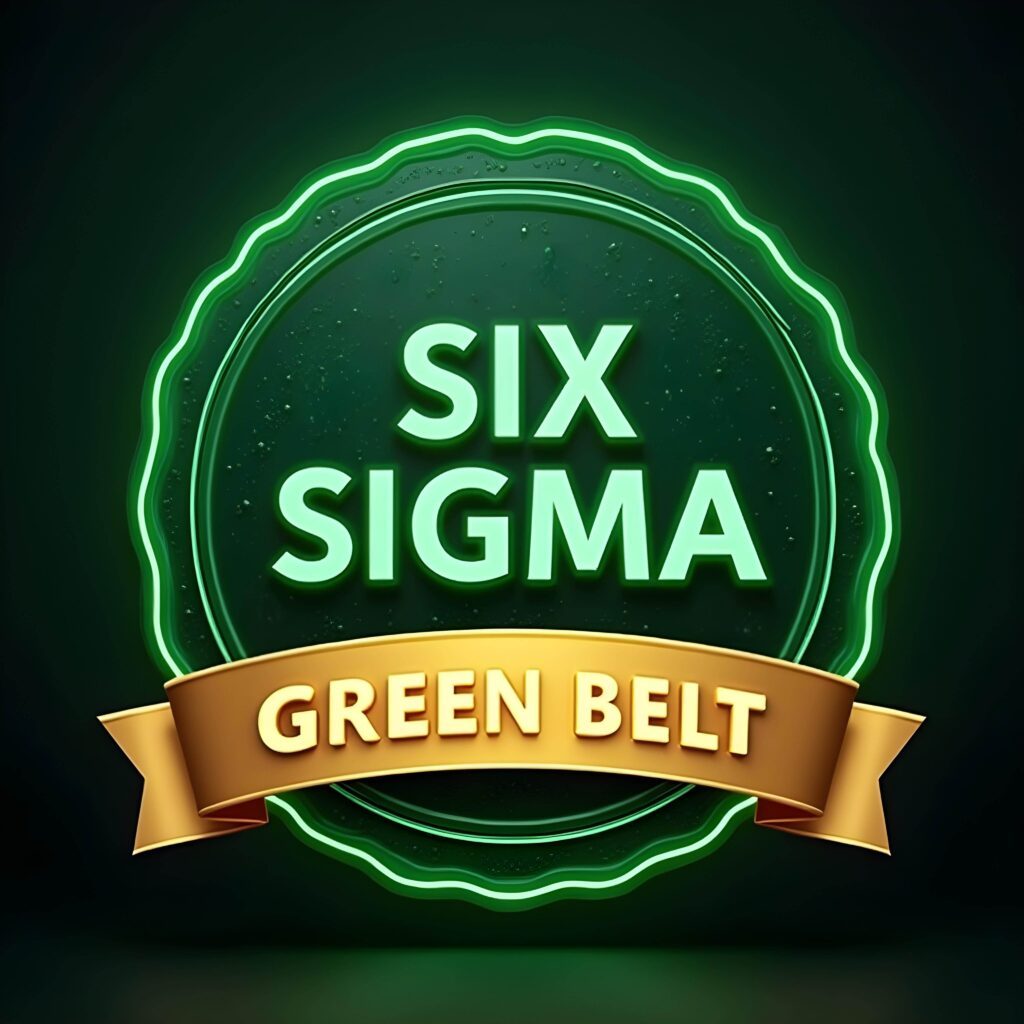
The Ultimate Guide to Six Sigma Green Belt : From Novice to Process Improvement Leadership
You’re in another team meeting. The same cycle plays out missed targets, rising costs, customer complaints piling up. Everyone is frustrated, but no one really knows what to do about it.
Your boss turns to you. “Can you look into this? See if we can find a solution?”
You nod. But inside, you’re thinking: Where do I even start?
If you’ve ever found yourself in this situation wanting to fix problems but not having the right approach to do it then Six Sigma Green Belt training is exactly what you need.
This guide will break down what you’ll actually learn in Green Belt Certification, how it helps you lead process improvement initiatives, and how it turns you from someone who sees problems into someone who solves them.
What is Six Sigma Green Belt?
A Six Sigma Green Belt is someone who identifies and eliminates process inefficiencies using quality improvement methods and statistical process control.
Think of it like this:
- Problems in business aren’t always obvious.
- Many companies guess at solutions instead of finding root causes.
- Six Sigma Green Belt professionals use DMAIC methodology and statistical tools to diagnose and fix problems that cost money, waste time, and frustrate customers.
This isn’t just about learning a few tools. It’s about learning a systematic, repeatable approach that makes you a problem-solving expert.
Here’s what you’ll actually learn.
1. Mastering the DMAIC Methodology
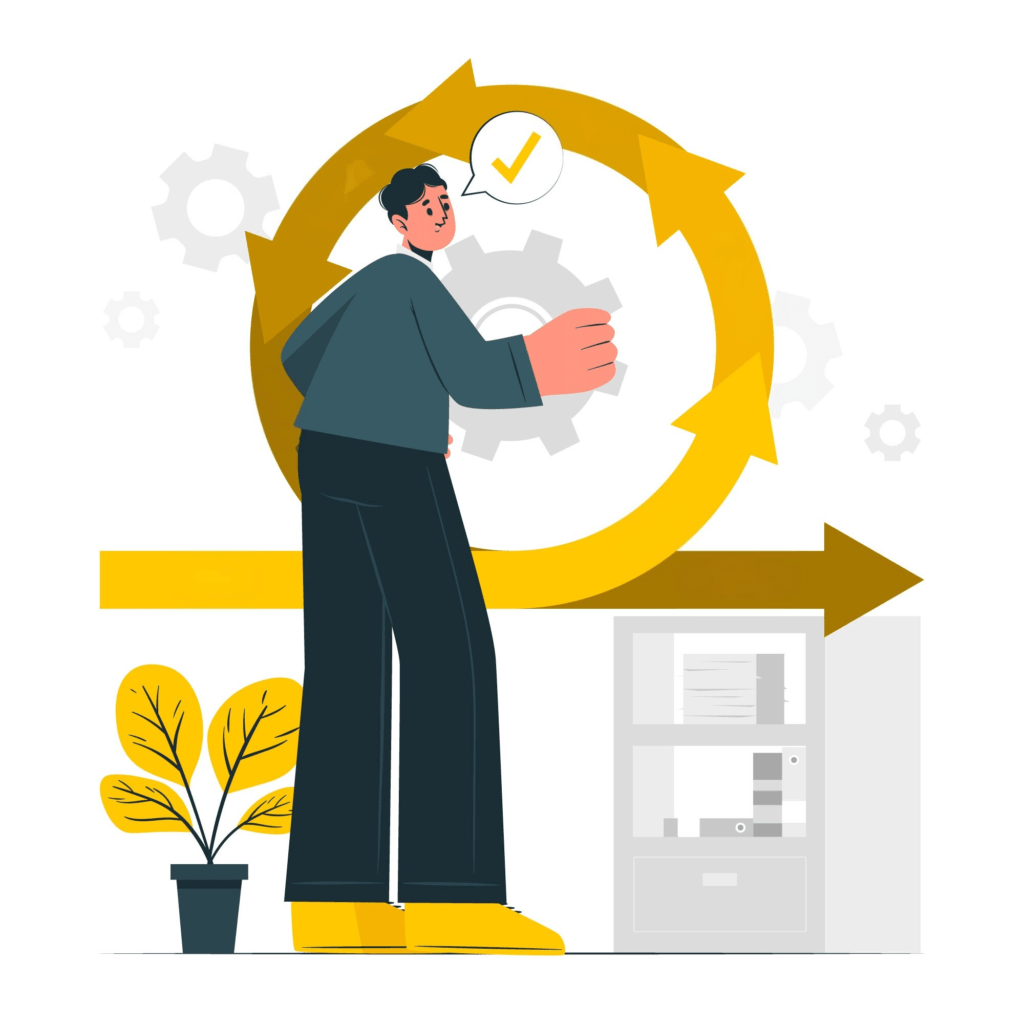
The backbone of Six Sigma Green Belt training is DMAIC methodology a five-phase problem-solving framework.
Six Sigma Green Belt professionals use DMAIC to fix business problems at their root instead of just applying short-term fixes. But what exactly is DMAIC?
- Define – Clearly identify the problem. What’s broken? Who’s affected? What is the goal?
- Measure – Collect data to understand the current situation. How bad is the problem?
- Analyze – Find the real cause of the issue. What’s actually driving the problem?
- Improve – Develop and test solutions. How do we fix it permanently?
- Control – Ensure the problem stays fixed. What systems do we put in place to sustain the improvement?
Without DMAIC, companies waste time chasing symptoms instead of solving causes.
You’ll learn how to take a chaotic, recurring issue and turn it into a clear, structured plan for solving it permanently.
2. How to Collect and Analyze Data to Solve Problems
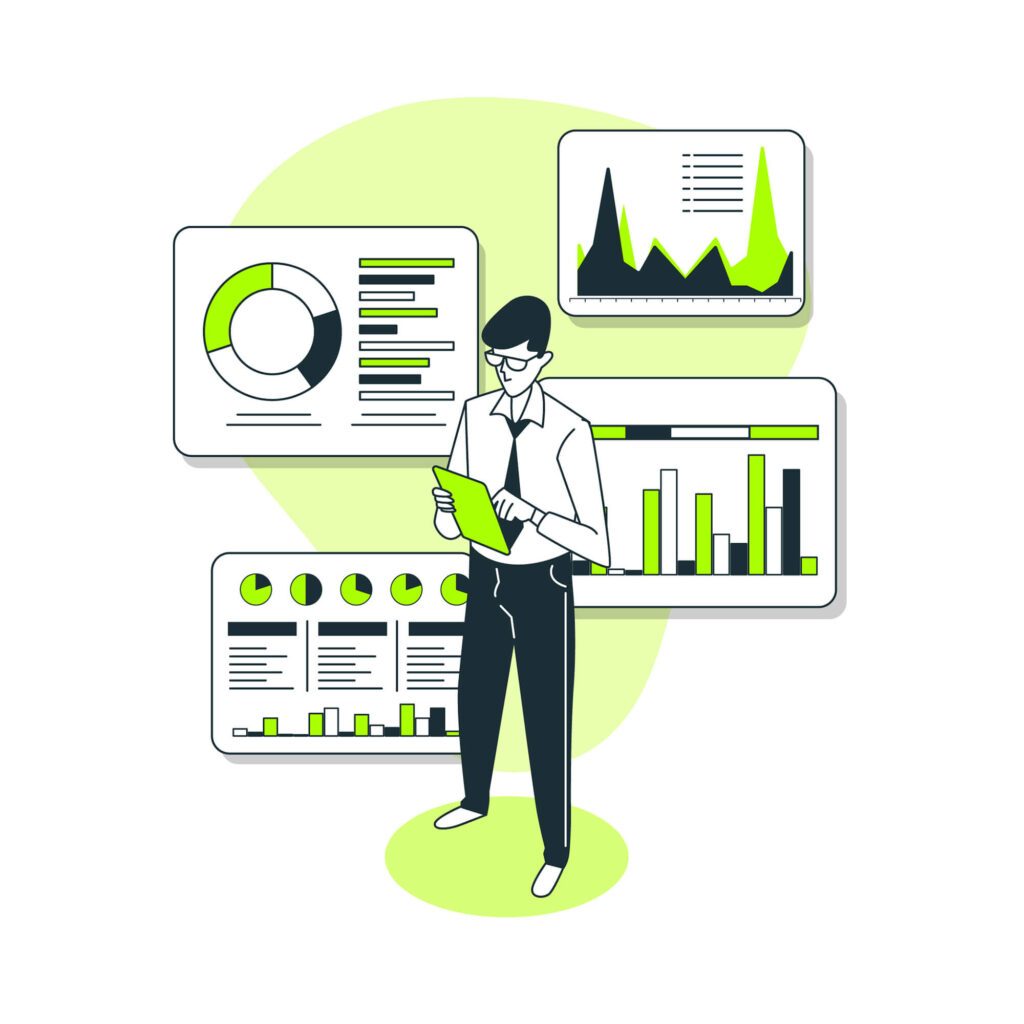
Imagine your team is arguing about why production delays keep happening.
- One person says it’s a supplier issue.
- Another blames outdated machinery.
- Someone else thinks it’s a staffing problem.
Who’s right?
That’s where statistical process control comes in.
Green Belt Certification teaches you how to collect and interpret data so you’re not relying on opinions you’re using facts.
You’ll learn:
- How to define the right metrics so you’re measuring what actually matters.
- How to use sampling techniques to get reliable data without analyzing everything.
- How to apply Measurement System Analysis (MSA) to ensure your data is accurate.
By the time you’re done, you won’t just be guessing what’s wrong you’ll have data that proves it.
3. Statistical Tools Every Six Sigma Green Belt Uses
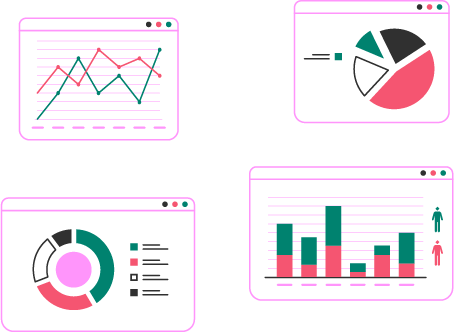
A lot of people assume Six Sigma Green Belt is all about math.
The truth? It’s about making smart decisions with statistical process control.
As a Six Sigma Green Belt, you’ll use statistical tools to answer questions like:
- “Did this process change actually improve performance?” → Use Hypothesis Testing
- “What’s causing delays in production?” → Use Pareto Analysis to identify the biggest factor
- “Are defect rates getting worse over time?” → Use Control Charts to detect process changes
- “How well is our process meeting customer expectations?” → Use Capability Analysis (Cp, Cpk)
You don’t need to be a statistician. You just need to know which tool to use in which situation and that’s exactly what you’ll learn.
4. Understanding Process Variation and Reducing Waste
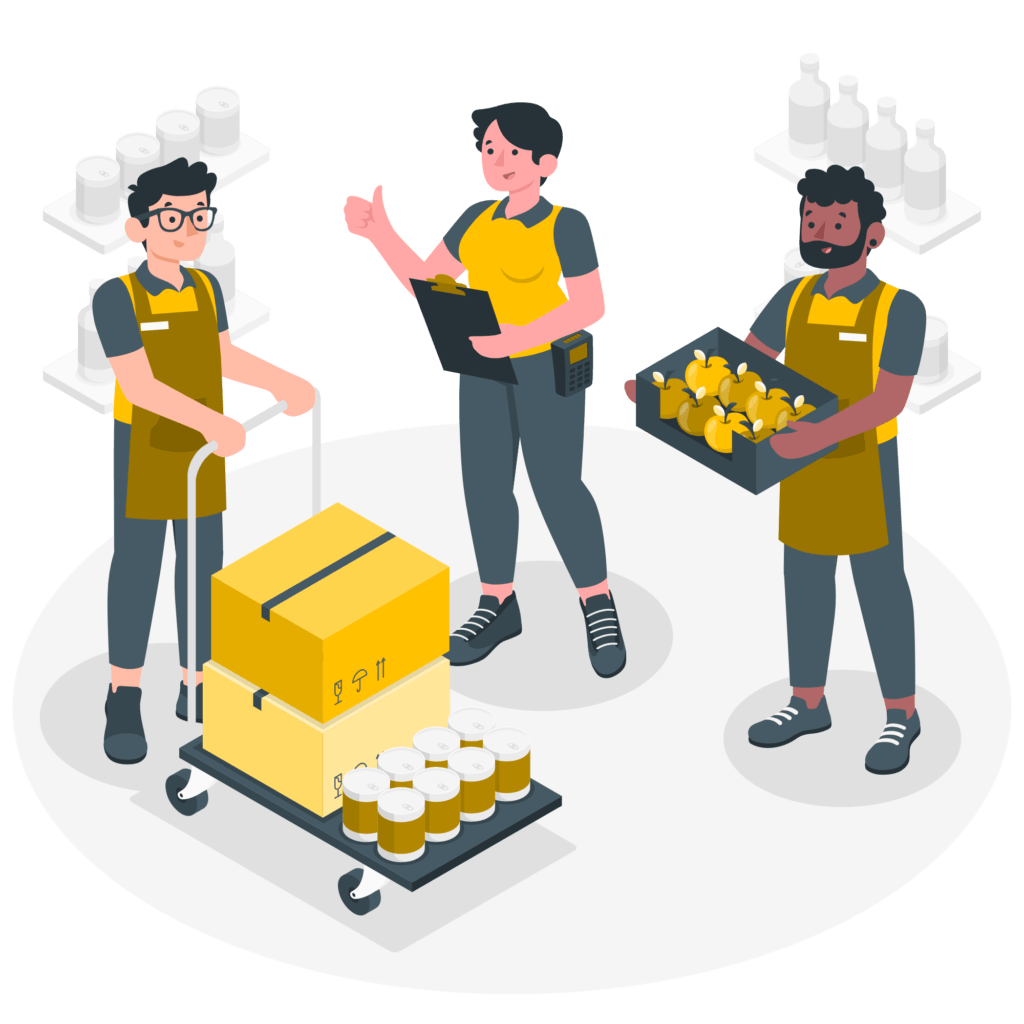
One of the biggest focuses in Six Sigma Green Belt training is understanding variation and waste.
Variation is the enemy of efficiency. If a process is unpredictable, it leads to:
- Missed deadlines
- Customer dissatisfaction
- Increased costs
Six Sigma Green Belt professionals learn how to:
- Identify common and special causes of variation
- Reduce process inconsistencies using statistical process control
- Apply Lean principles to eliminate unnecessary waste
This means cutting down on overproduction, excess inventory, unnecessary motion, and time delays all of which drain resources.
5. Leading Process Improvement Projects
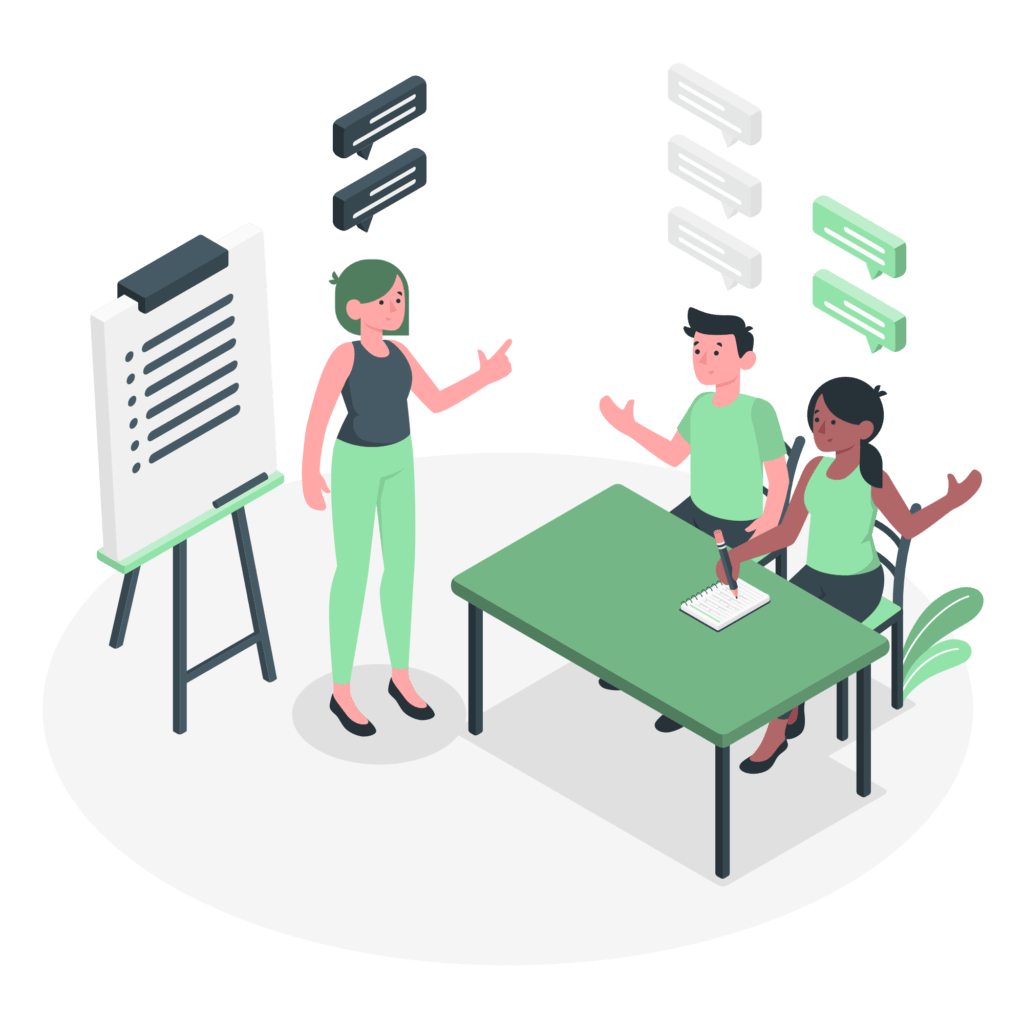
Solving problems is one thing. Getting people to accept the solution? That’s another.
A big part of Green Belt Certification focuses on process improvement leadership getting buy-in from teams, managers, and executives.
You’ll learn:
- How to structure a Six Sigma Green Belt project so it actually gets finished.
- How to communicate findings in a way that leadership pays attention to.
- How to manage resistance when people push back against change.
Because a solution is worthless if no one follows it.
Six Sigma Green Belt professionals don’t just crunch numbers they get people to act.
6. The ROI of a Green Belt Certification

Now you might be wondering why should you care about all of this?
Because Green Belt Certification isn’t just about fixing things at work. It’s about career transformation.
Once you have these skills, you become the go-to person when things go wrong.
- Your boss stops ignoring your suggestions.
- You get invited to bigger conversations.
- You don’t just participate in meetings you lead them.
Companies value process improvement leadership. Which means Green Belt Certification dies not add only another line on your resume it’s a ticket to bigger opportunities.
Industry Recognition and Career Growth
Beyond the professional benefits, Six Sigma Green Belt training improves your ability to:
- Think critically – Break down complex problems into manageable steps.
- Solve problems efficiently – Find the best solutions with a data-driven approach.
- Communicate ideas clearly – Present findings in a way that gets people to listen.
You also become part of a growing network of professionals specializing in quality improvement methods. This community opens doors to:
- New job roles
- Promotions
- Industry recognition
Green Belt Certification is also a stepping stone to higher Six Sigma levels like Black Belt and Master Black Belt, which lead to executive roles in process improvement.
7. Industries Using Six Sigma Green Belt
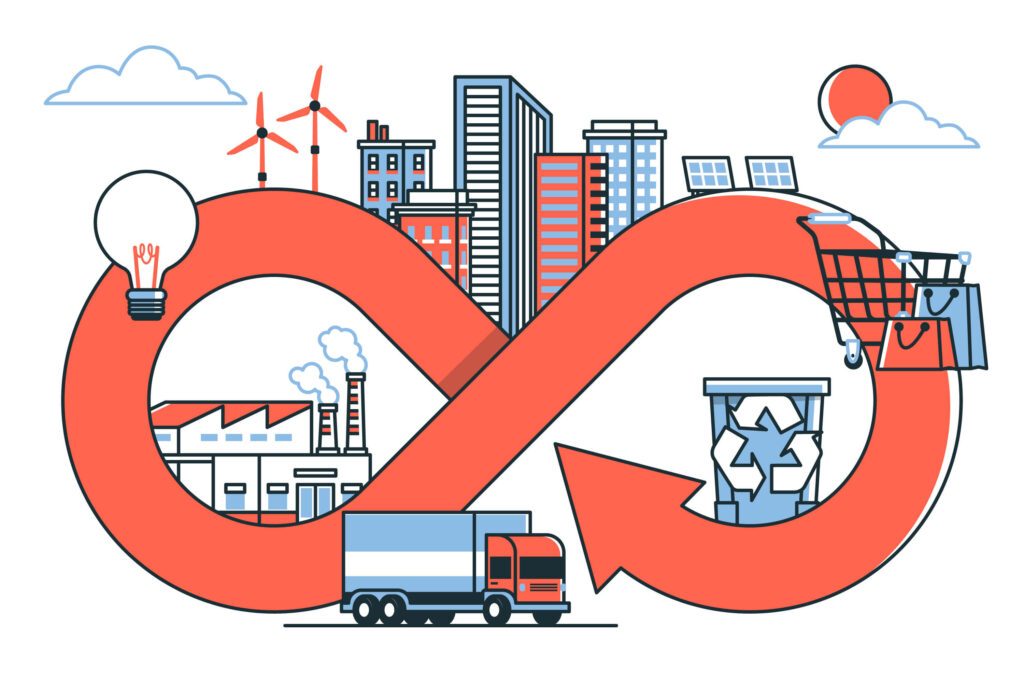
Six Sigma Green Belt isn’t just theory it’s a practical skillset used across industries to drive efficiency and improve quality. Businesses in manufacturing, healthcare, finance, IT, logistics, and even retail apply Six Sigma methodologies to reduce costs and enhance customer satisfaction.
Manufacturing:
Companies like General Electric and Toyota use Six Sigma to reduce defects, optimize production processes, and minimize waste. A Green Belt professional might identify the root cause of defective products and implement solutions that prevent errors from happening in the first place.
Healthcare:
Hospitals and clinics use Six Sigma to streamline patient flow, reduce wait times, and minimize medical errors. A Green Belt might analyze data on patient admissions and improve scheduling systems to ensure faster service.
Finance & Banking:
Banks use Six Sigma to reduce transaction errors, improve customer service, and enhance compliance processes. A Green Belt can lead projects that lower processing times for loan approvals or credit card applications.
IT & Software Development:
Green Belts in IT improve software development cycles, reduce bugs, and optimize project management. They apply Six Sigma principles to detect inefficiencies in coding processes and enhance software reliability.
No matter the industry, Six Sigma Green Belt professionals are problem-solvers who drive measurable improvements. The ability to apply data-driven decision-making makes them invaluable to organizations aiming for efficiency and excellence.
8. Overcoming Challenges as a Six Sigma Green Belt
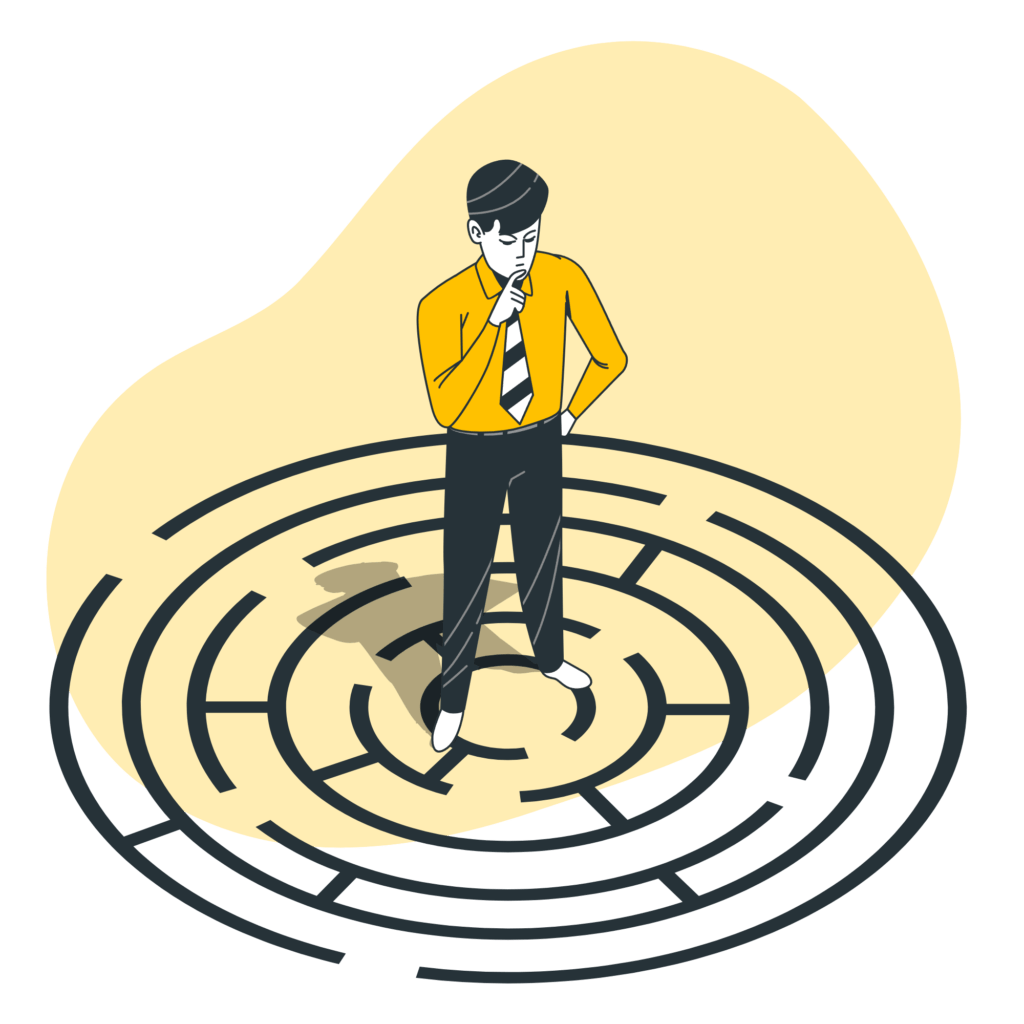
While Six Sigma Green Belt training provides powerful tools for solving problems, applying these concepts in real-world scenarios comes with challenges. Understanding these obstacles and knowing how to navigate them is essential for success.
1. Resistance to Change
One of the biggest hurdles is getting teams and leadership on board with process improvements. People are often comfortable with existing workflows, even if they are inefficient. Green Belt professionals must develop strong communication and leadership skills to help teams understand the benefits of change and drive engagement.
2. Data Collection Issues
Not all organizations have structured data collection systems. You might find incomplete, inaccurate, or inconsistent data, making analysis difficult. Green Belts must learn to work with what’s available leveraging sampling techniques, measurement system analysis, and data validation to ensure they base decisions on reliable information.
3. Balancing Six Sigma with Daily Responsibilities
Many Green Belt professionals work on Six Sigma projects while managing their regular job duties. Prioritizing tasks, setting clear project timelines, and using effective project management techniques ensure that improvements don’t get delayed due to day-to-day workload pressures.
4. Sustaining Improvements
Fixing a process is one thing, but ensuring that improvements last is another challenge. Without proper Control Phase implementation, organizations risk falling back into old habits. Green Belts must focus on standardization, documentation, and continuous monitoring to maintain long-term success.
By addressing these challenges proactively, Six Sigma Green Belt professionals increase their impact and build a reputation as trusted problem-solvers.
Final Thoughts
Six Sigma Green Belt is not confined to only knowing DMAIC methodology or learning statistical process control.
It’s about becoming a leader someone who can take any messy, frustrating business problem and turn it into a structured, lasting solution.
It’s about stepping up, solving problems, and making an impact that people notice.
So, are you ready to stop watching problems… and start solving them?